Industrial mechanical arm automatic control method based on deep reinforcement learning
A technology for reinforcement learning, industrial machinery, applied in neural learning methods, adaptive control, manipulators, etc.
- Summary
- Abstract
- Description
- Claims
- Application Information
AI Technical Summary
Problems solved by technology
Method used
Image
Examples
Embodiment Construction
[0042] The present invention will be further described in detail below in conjunction with the accompanying drawings and specific embodiments.
[0043] Such as figure 1 Shown is a schematic flow chart of an automatic control method for industrial manipulators based on deep reinforcement learning, including the following steps:
[0044] Step 1) Build a deep reinforcement learning model
[0045] 1.1) Experience pool initialization: set the experience pool as a two-dimensional matrix with m rows and n columns, and initialize the value of each element in the two-dimensional matrix to 0, where m is the size of the sample and n is the information stored in each sample Quantity, n=2×state_dim+action_dim+1, state_dim is the dimension of the state, action_dim is the dimension of the action; at the same time, reserve space for storing reward information in the experience pool, n=2×state_dim+action_dim+1 1 in this formula is the reserved space for storing reward information;
[0046] ...
PUM
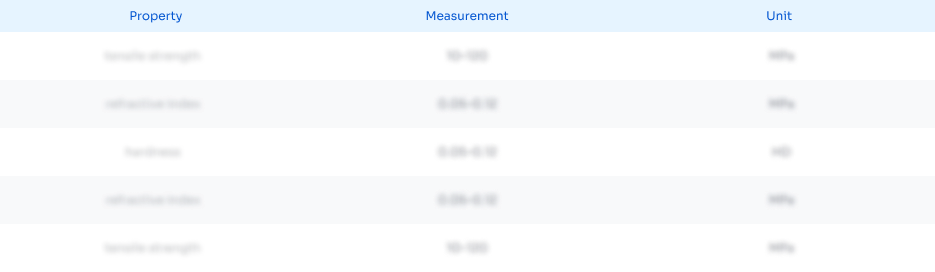
Abstract
Description
Claims
Application Information

- Generate Ideas
- Intellectual Property
- Life Sciences
- Materials
- Tech Scout
- Unparalleled Data Quality
- Higher Quality Content
- 60% Fewer Hallucinations
Browse by: Latest US Patents, China's latest patents, Technical Efficacy Thesaurus, Application Domain, Technology Topic, Popular Technical Reports.
© 2025 PatSnap. All rights reserved.Legal|Privacy policy|Modern Slavery Act Transparency Statement|Sitemap|About US| Contact US: help@patsnap.com