Six-pole mixed magnetic bearing
A hybrid magnetic bearing and axial technology, applied in the field of machinery and electrical transmission, can solve the problems of reduced magnetic bearing performance, low degree of freedom coupling, large drive circuit size, etc., to reduce manufacturing and operating costs, and reduce the number of switch tubes , the effect of saving radial space
- Summary
- Abstract
- Description
- Claims
- Application Information
AI Technical Summary
Problems solved by technology
Method used
Image
Examples
Embodiment Construction
[0020] Such as figure 1 As shown, the present invention is made up of rotating shaft 8, rotor 7, permanent magnet 10, left stator core 1, right stator core 2 and control coil 3. The center of the present invention is the rotating shaft 8, the outer coaxial fixed sleeve of the rotating shaft 8 has the rotor 7, the outer coaxial sleeve of the rotor 7 has the left stator core 1 and the right stator core 2, and the structure of the left stator core 1 and the right stator core 2 is the same, but Arranged symmetrically on the left and right in the axial direction. The left end and the right end of the rotor 7 are respectively provided with a force plate, which are respectively the left force plate 17 and the right force plate 18. The two force plates are coaxial with the rotor 7 and have the same structure. The outer diameters of the two force plates are Larger than the outer diameter of the rotor 7, the two stressed disks can be integrated with the rotor 7. The same radial air ga...
PUM
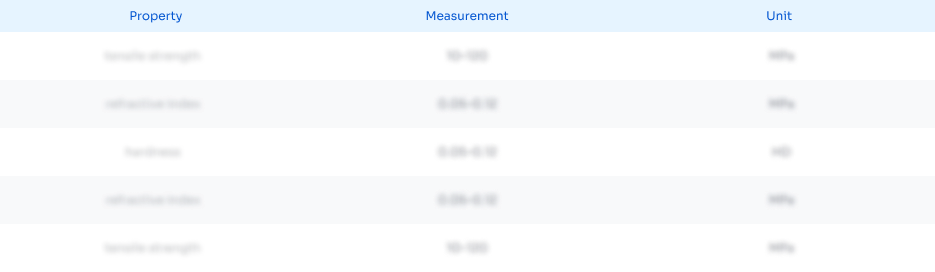
Abstract
Description
Claims
Application Information

- R&D Engineer
- R&D Manager
- IP Professional
- Industry Leading Data Capabilities
- Powerful AI technology
- Patent DNA Extraction
Browse by: Latest US Patents, China's latest patents, Technical Efficacy Thesaurus, Application Domain, Technology Topic, Popular Technical Reports.
© 2024 PatSnap. All rights reserved.Legal|Privacy policy|Modern Slavery Act Transparency Statement|Sitemap|About US| Contact US: help@patsnap.com