Prefabricated concrete frame beam-column joint construction method
A technology for precast concrete, beam-column joints, applied in columns, joists, girders, etc., can solve the problems of cast-in-place concrete polluting the environment, low resource utilization, insufficient seismic performance, etc. , the effect of simple and quick connection
- Summary
- Abstract
- Description
- Claims
- Application Information
AI Technical Summary
Problems solved by technology
Method used
Image
Examples
Embodiment Construction
[0022] In order to further understand the invention content, characteristics and effects of the present invention, the following examples are given, and detailed descriptions are as follows in conjunction with the accompanying drawings:
[0023] see Figure 1 to Figure 6 , a prefabricated concrete frame beam-column joint construction method, the frame column is a prefabricated column 2, adopts a reinforced concrete structure, the frame beam adopts a composite beam 1, and the composite beam 1 adopts a reinforced concrete structure, and is provided with prefabricated beams 1-5 and the post-casting part, the composite beam stirrup 1-2 protrudes above the top surface of the prefabricated beam 1-5, and a beam end keyway 1-4 is prefabricated on the upper part of the beam end of the prefabricated beam 1-5, A connection plate 3-1 is embedded in the lower part of the beam end of the prefabricated beam 1-5, and a connection installation groove 1-6 is prefabricated at the bottom of the b...
PUM
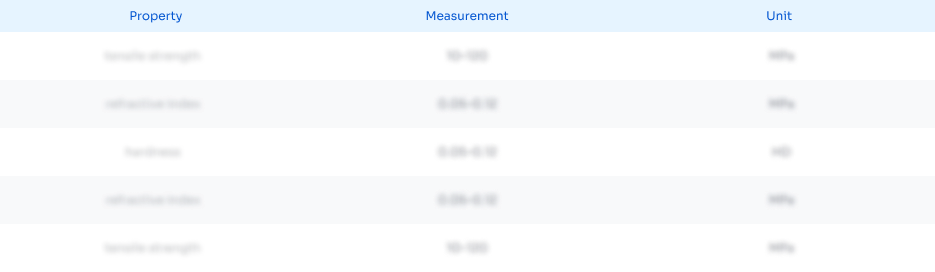
Abstract
Description
Claims
Application Information

- R&D
- Intellectual Property
- Life Sciences
- Materials
- Tech Scout
- Unparalleled Data Quality
- Higher Quality Content
- 60% Fewer Hallucinations
Browse by: Latest US Patents, China's latest patents, Technical Efficacy Thesaurus, Application Domain, Technology Topic, Popular Technical Reports.
© 2025 PatSnap. All rights reserved.Legal|Privacy policy|Modern Slavery Act Transparency Statement|Sitemap|About US| Contact US: help@patsnap.com