A Secondary Condensation Method for Spacecraft Finite Element Model
A finite element and spacecraft technology, applied in the field of secondary polycondensation of spacecraft finite element models
- Summary
- Abstract
- Description
- Claims
- Application Information
AI Technical Summary
Problems solved by technology
Method used
Image
Examples
Embodiment Construction
[0064] Some details in the technical solution of the present invention will be further described below in conjunction with the accompanying drawings and a specific embodiment.
[0065] A secondary polycondensation method for a spacecraft finite element model, the process is as follows figure 1 shown, including the following steps:
[0066] Step 1, use MSC.Patran software to establish the finite element physical model of the main structure of the satellite in the launch state, such as figure 2 As shown, the satellite adopts the main structure of "central load-bearing tube + box-plate type", and the finite element physical model of the main structure is modeled by shell elements, with a total of 24,567 nodes and 25,134 units; among them, the central load-bearing tube axial It is parallel to the Z axis of the satellite coordinate system, and the X and Y directions of the coordinate system are respectively parallel to the two normal directions of the satellite deck; the payload ...
PUM
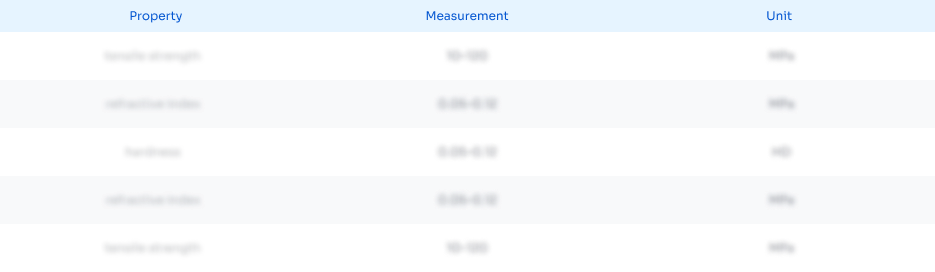
Abstract
Description
Claims
Application Information

- R&D
- Intellectual Property
- Life Sciences
- Materials
- Tech Scout
- Unparalleled Data Quality
- Higher Quality Content
- 60% Fewer Hallucinations
Browse by: Latest US Patents, China's latest patents, Technical Efficacy Thesaurus, Application Domain, Technology Topic, Popular Technical Reports.
© 2025 PatSnap. All rights reserved.Legal|Privacy policy|Modern Slavery Act Transparency Statement|Sitemap|About US| Contact US: help@patsnap.com