System and method for converting biomass raw material into clean diesel
A biomass raw material and biomass technology, applied in the direction of waste fuel, liquid hydrocarbon mixture preparation, gasification process, etc., can solve the problems of high energy consumption of tail gas cycle, complicated process, fluid drift, etc., and achieve good hydrogenation effect, The effect of short process flow and easy processing
- Summary
- Abstract
- Description
- Claims
- Application Information
AI Technical Summary
Problems solved by technology
Method used
Image
Examples
Embodiment 1
[0061] use figure 1 The system shown, processes biomass feedstock. The biomass raw material is corncob. After crushing and drying, the corncobs are fed into the fluidized bed gasification furnace in the form of particles with a diameter of 15 mm. The air-steam feed equivalence ratio is 0.3, the reaction temperature is 950 ° C, and the reaction pressure is 0.5 MPa. The composition of the obtained crude synthesis gas is shown in Table 1. The crude synthesis gas passes through the purification unit to remove the sulfur in the synthesis gas, and the removed tar is used as fuel oil for heating. The purified syngas is pressurized and enters the Fischer-Tropsch synthesis reaction unit. The reaction is carried out in the Fischer-Tropsch synthesis reactor described in the present invention. Fischer-Tropsch synthesis reactor as attached figure 2 shown. The reactor is processed by plate brazing method. Respectively process the reaction channel layer plate, the fluid channel layer...
Embodiment 2
[0076] In the Fischer-Tropsch synthesis reaction unit, react in the Fischer-Tropsch synthesis reactor of the present invention, and the Fischer-Tropsch synthesis reactor is as figure 2 shown. The Fischer-Tropsch synthesis reactor is processed by plate brazing method. Respectively process the reaction channel layer plate, the fluid channel layer plate, the upper cover plate and the lower cover plate. The reaction channel is a linear channel with a length of 100 mm, a width of 10 mm, a depth of 1 mm, and a left and right interval of 5 mm. The fluid channel is 60mm long and 1mm deep, and adopts a scaled shape, such as figure 2 As shown, the maximum width is 8mm and the minimum width is 5mm. 1 upper cover plate, 10 reaction channel laminates, 11 fluid channel laminates, and 1 lower cover plate are welded together by high-temperature brazing, and the brazing material is alloy Al-20Cu-10Si-2Ni. Reactor unit specific surface area 1100m 2 / m 3 , the ratio of fluid channel area...
Embodiment 3
[0079] In the Fischer-Tropsch synthesis reaction unit, react in the Fischer-Tropsch synthesis reactor of the present invention, and the Fischer-Tropsch synthesis reactor is as Figure 4 shown. The reactor is processed by high-temperature diffusion welding of plates. Respectively process the reaction channel layer plate, the fluid channel layer plate, the upper cover plate and the lower cover plate. The reaction channel is a linear channel with a length of 400 mm, a width of 10 mm, a depth of 1 mm, and a left and right interval of 5 mm. The fluid channel is 400mm long, 5mm wide, and 1mm deep, and adopts a broken line shape, such as figure 2 As shown, the angle of the broken line is 105°, the length of the broken line unit is 20mm, the length of the straight channel at both ends is 10mm, and the channel interval is 5mm. 1 upper cover plate, 10 reaction channel laminates, 11 fluid channel laminates, and 1 lower cover plate are welded together by high temperature diffusion wel...
PUM
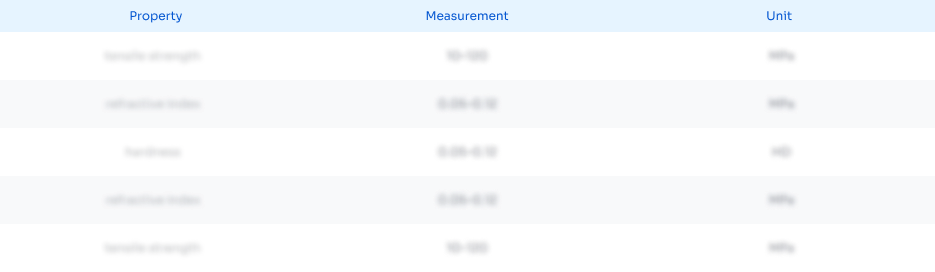
Abstract
Description
Claims
Application Information

- Generate Ideas
- Intellectual Property
- Life Sciences
- Materials
- Tech Scout
- Unparalleled Data Quality
- Higher Quality Content
- 60% Fewer Hallucinations
Browse by: Latest US Patents, China's latest patents, Technical Efficacy Thesaurus, Application Domain, Technology Topic, Popular Technical Reports.
© 2025 PatSnap. All rights reserved.Legal|Privacy policy|Modern Slavery Act Transparency Statement|Sitemap|About US| Contact US: help@patsnap.com