Support for double-camera assembly, split support type double-camera assembly and assembling method
An assembly method and a bracket-type technology, which are applied to the machine table/bracket, supporting machine, camera body, etc., can solve the problems of high scrapping cost, inability to further adjust the accuracy, affecting positioning accuracy, etc., and reduce maintenance or scrapping costs. Effect
- Summary
- Abstract
- Description
- Claims
- Application Information
AI Technical Summary
Problems solved by technology
Method used
Image
Examples
Embodiment 1
[0031] Such as figure 1 As shown, this embodiment provides a bracket for dual-camera, including a bracket body 1, and the bracket body 1 is provided with a first positioning hole 101, a second positioning hole 102, and four housing positioning locking points 103 and four PCB board positioning locking points 104; the bracket body 1 is made of magnesium-aluminum alloy material.
[0032] The first positioning hole 101 is used to fix the first lens module, and a first gap for calibration is reserved between the first positioning hole 101 and the first lens module;
[0033] The second positioning hole 102 is used to fix the second lens module, and a second gap for calibration is reserved between the second positioning hole 102 and the second lens module;
[0034] The housing positioning and locking points 103 are used to fix the bracket body 1 on the housing, wherein two of the housing positioning locking points 103 are arranged at one end of the bracket body 1, and the other two ...
Embodiment 2
[0040] Such as figure 2 As shown, this embodiment provides a split bracket type dual camera, including a first lens module 2, a second lens module 3 and the bracket 4 described in Embodiment 1, the first lens module 2 is fixed Connected to the first positioning hole, the second lens module 3 is fixed to the second positioning hole.
[0041] The split-bracket dual-camera provided in this embodiment can meet the requirements of different Sensor SMT processes. Whether the Sensor adopts CSP (Chip Scale Package, chip scale package), COB (Chips on Board, chip on board package), PLCC (Plastic Leaded Chip Carrier, special pin chip package) and other packages, all can meet the relevant parameters. In addition, it can also meet the design requirements of different Lens. Regardless of the difference between Lens and Holder design, almost all of them can achieve the design process precision, without having to open the Holder mold separately.
[0042]In this embodiment, during use of t...
Embodiment 3
[0044] Such as image 3 As shown, this embodiment provides a method for assembling the split bracket type dual camera for assembling the split bracket type dual camera described in Example 2. The assembly method includes the following steps:
[0045] Step 101, fixing the first lens module to the first positioning hole with colloid;
[0046] Step 102: Set the second lens module in the second positioning hole and perform positioning calibration using the AA process to determine a target position, the target position makes the first lens module and the second The lens module meets the requirements of positioning accuracy;
[0047] Step 103 , fixing the second lens module at the target position in the second positioning hole with colloid.
[0048] In this embodiment, in order to achieve the required accuracy, the AA process is used for calibration during the assembly process. The assembly method is to fix the first lens module in advance, and adjust the second lens module throug...
PUM
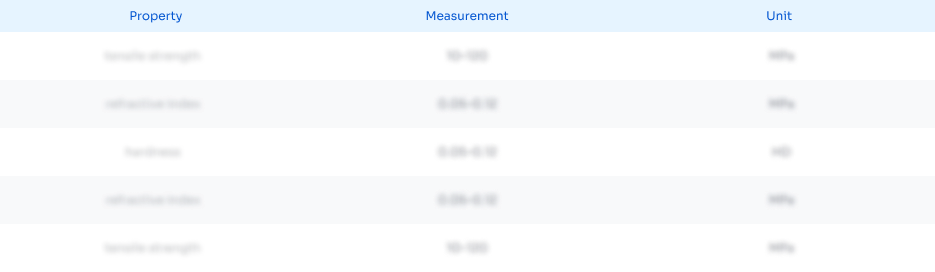
Abstract
Description
Claims
Application Information

- Generate Ideas
- Intellectual Property
- Life Sciences
- Materials
- Tech Scout
- Unparalleled Data Quality
- Higher Quality Content
- 60% Fewer Hallucinations
Browse by: Latest US Patents, China's latest patents, Technical Efficacy Thesaurus, Application Domain, Technology Topic, Popular Technical Reports.
© 2025 PatSnap. All rights reserved.Legal|Privacy policy|Modern Slavery Act Transparency Statement|Sitemap|About US| Contact US: help@patsnap.com