Method for preparing flame-retardant flexible freight bag
A technology for container bags and flame retardants, which is applied in the manufacture of fire-retardant and flame-retardant filaments, rayon manufacturing, and single-component polyolefin rayon. The effect of improving combustion performance and improving uniformity
- Summary
- Abstract
- Description
- Claims
- Application Information
AI Technical Summary
Problems solved by technology
Method used
Examples
Embodiment 1
[0015] A method for preparing a flame-retardant container bag, comprising the following steps:
[0016] (1) In parts by weight, after mixing 32 parts of melamine cyanurate, 10 parts of sodium molybdate dihydrate, 4 parts of N-octyldiaminoethylglycine hydrochloride, and 11 parts of polyvinylimidazole, Add it to a ball mill, and after ball milling for 2 hours, dry it to obtain a flame retardant;
[0017] (2) In parts by weight, after mixing 85 parts of polypropylene resin, 3 parts of flame retardant, 1 part of N-acetylthiourea, and 3-5 parts of mixed additives, they are added to the extruder, melt-spun, and then After being woven into suspenders and base fabrics on a loom, they are cut and sewn to make flame-retardant container bags.
[0018] Specifically, in the above step (1), the drying temperature is 65°C.
[0019] Specifically, in the above step (1), the rotational speed of the ball milling treatment is 250 r / min.
[0020] Specifically, in the above step (2), the mixed a...
Embodiment 2
[0022] A method for preparing a flame-retardant container bag, comprising the following steps:
[0023] (1) In parts by weight, after mixing 34 parts of melamine cyanurate, 13 parts of sodium molybdate dihydrate, 6 parts of N-octyldiaminoethylglycine hydrochloride, and 13 parts of polyvinylimidazole, Add it to a ball mill, and after ball milling for 2.5 hours, dry it to obtain a flame retardant;
[0024] (2) In parts by weight, after mixing 94 parts of polypropylene resin, 5 parts of flame retardant, 2 parts of N-acetylthiourea, and 4 parts of mixed additives, they are added to the extruder, melt-spun, and then woven After machine weaving into suspenders and base fabrics, they are cut and sewn to make flame-retardant container bags.
[0025] Specifically, in the above step (1), the drying temperature is 68°C.
[0026] Specifically, in the above step (1), the rotational speed of the ball milling treatment is 280 r / min.
[0027] Specifically, in the above step (2), the mixed ...
Embodiment 3
[0029] A method for preparing a flame-retardant container bag, comprising the following steps:
[0030] (1) In parts by weight, after mixing 36 parts of melamine cyanurate, 15 parts of sodium molybdate dihydrate, 9 parts of N-octyldiaminoethylglycine hydrochloride, and 16 parts of polyvinylimidazole, Add it into a ball mill, and after ball milling for 3 hours, dry it to obtain a flame retardant;
[0031] (2) In parts by weight, after mixing 98 parts of polypropylene resin, 6 parts of flame retardant, 3 parts of N-acetylthiourea, and 3-5 parts of mixed additives, they are added to the extruder, melt-spun, and then After being woven into suspenders and base fabrics on a loom, they are cut and sewn to make flame-retardant container bags.
[0032] Specifically, in the above step (1), the drying temperature is 70°C.
[0033] Specifically, in the above step (1), the rotational speed of the ball milling treatment is 300 r / min.
[0034] Specifically, in the above step (2), the mixe...
PUM
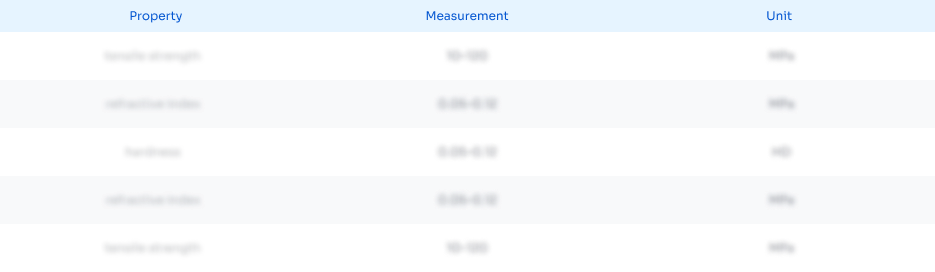
Abstract
Description
Claims
Application Information

- R&D
- Intellectual Property
- Life Sciences
- Materials
- Tech Scout
- Unparalleled Data Quality
- Higher Quality Content
- 60% Fewer Hallucinations
Browse by: Latest US Patents, China's latest patents, Technical Efficacy Thesaurus, Application Domain, Technology Topic, Popular Technical Reports.
© 2025 PatSnap. All rights reserved.Legal|Privacy policy|Modern Slavery Act Transparency Statement|Sitemap|About US| Contact US: help@patsnap.com