Method for quickly preparing double-mounting plate blade
A technology of double mounting plates and mounting plates, which is applied in the field of aeroengine compressor rotors and stator blades, can solve problems such as inability to realize precision milling, unstable process control, and poor blade shape consistency, shortening the development cycle and reducing fixture manufacturing The effect of increasing the difficulty and pass rate
- Summary
- Abstract
- Description
- Claims
- Application Information
AI Technical Summary
Problems solved by technology
Method used
Image
Examples
Embodiment 1
[0032] A method for quickly preparing double mounting plate blades, characterized in that the process is:
[0033] 1) Process the upper and lower ends of the process table: process a process table at the upper and lower ends of the blade blank, the upper process table is connected to the blade tenon or the outer side of the upper mounting plate, and the lower process table is connected to the outer side of the lower mounting plate of the blade; The process table at both ends is designed as a cuboid structure, and the size is length, width and height: 15mm×10mm×15mm;
[0034] 2) The clamping structure is designed based on the craft table at the upper and lower ends;
[0035] 3) Rough / finish milling of the mounting plate and the airfoil profile based on the upper and lower ends of the process table;
[0036] 4) Polishing the airfoil surface;
[0037] 5), wire cutting removes the upper and lower ends of the blade (can be removed by means of removal), and then uses the conventio...
Embodiment 2
[0040] The difference from Embodiment 1 is that the upper and lower process tables are designed as cylindrical structures, and the dimensions are designed as follows: diameter and height are Φ10mm×15mm.
Embodiment 3
[0042] The difference from Example 1 is that the upper and lower ends of the process table are designed as a cuboid structure, and the size is 25mm x 15mm x 25mm in length, width and height; after step 3) rough milling and heat treatment for stress relief, the process table is deformed and arranged The reference process of repairing the craft table is established to ensure the accuracy of the precision milling and clamping positioning.
PUM
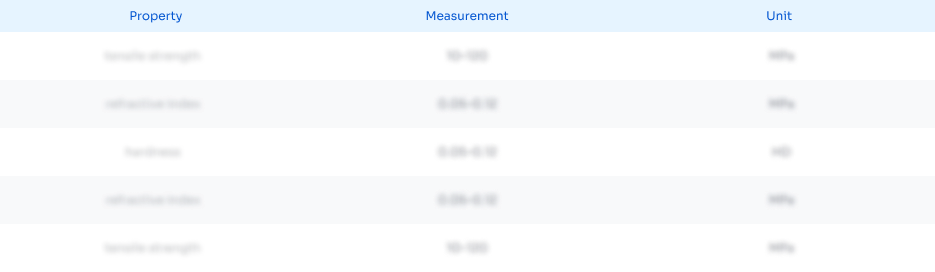
Abstract
Description
Claims
Application Information

- R&D
- Intellectual Property
- Life Sciences
- Materials
- Tech Scout
- Unparalleled Data Quality
- Higher Quality Content
- 60% Fewer Hallucinations
Browse by: Latest US Patents, China's latest patents, Technical Efficacy Thesaurus, Application Domain, Technology Topic, Popular Technical Reports.
© 2025 PatSnap. All rights reserved.Legal|Privacy policy|Modern Slavery Act Transparency Statement|Sitemap|About US| Contact US: help@patsnap.com