Black dye composition and application of black dye composition in wool dyeing
A black dye and composition technology, applied in the field of wool dyeing, can solve the problems of low price of disperse dyes, high price of reactive dyes, and difficulty in popularization and use, and achieve excellent solubilizing dyeing effect, good sublimation fastness, and good light exposure The effect of fastness
- Summary
- Abstract
- Description
- Claims
- Application Information
AI Technical Summary
Problems solved by technology
Method used
Image
Examples
Embodiment 1
[0054] 41g of component A shown in formula (I), 38g of component B shown in formula (II), 8g of component C shown in formula (III), and 10g of the group shown in formula (IV) Part D, 3g of component E represented by formula (IV) and 200g of additives are blended with water, ground and dispersed with a sand mill, and then spray-dried to obtain a finished dye.
[0055] In terms of mass percentage, the additives in this example include the following components: Pingpinga O-20 55%, polyoxyethylene-20 stearate 3%, triethylene glycol monobutyl ether 7%, octadecane Base betaine 8%, polyamide polyamine epichlorohydrin 7%, chitosan 5%, penetrant POWEZOL SUP 6%, leveling agent POWEZOL B 9%;
[0056] Among them, the average molecular weight of polyamide polyamine epichlorohydrin is 9000D; the degree of deacetylation of chitosan is 75%, and the average molecular weight is 4000D.
Embodiment 2
[0058] 30 g of component A shown in formula (I), 50 g of component B shown in formula (II), 14 g of component C shown in formula (III), and 4 g of the group shown in formula (IV) Part D, 2g of component E shown in formula (IV) and 150g of additives are blended with water, ground and dispersed with a sand mill, and then spray-dried to obtain a finished dye.
[0059] In terms of mass percentage, the additives in this example include the following components: Pingpinga O-15 45%, polyoxyethylene-20 stearate 4%, triethylene glycol monobutyl ether 8%, octadecane Base betaine 12%, polyamide polyamine epichlorohydrin 8%, chitosan 3%, penetrant POWEZOL SUP 14%, leveling agent POWEZOL B 6%;
[0060] Among them, the average molecular weight of polyamide polyamine epichlorohydrin is 8000D; the degree of deacetylation of chitosan is 80%, and the average molecular weight is 4000D.
Embodiment 3
[0062] 50g of component A shown in formula (I), 30g of component B shown in formula (II), 3g of component C shown in formula (III), and 13g of the group shown in formula (IV) Part D, 4g of component E shown in formula (IV) and 250g of additives are blended with water, ground and dispersed with a sand mill, and then spray-dried to obtain a finished dye.
[0063] In terms of mass percentage, the additives in this example include the following components: Pingpinga O-30 65%, polyoxyethylene-20 stearate 2%, triethylene glycol monobutyl ether 5%, octadecane Base betaine 6%, polyamide polyamine epichlorohydrin 8%, chitosan 3%, penetrant POWEZOL SUP 5%, leveling agent POWEZOL B 6%;
[0064] Among them, the average molecular weight of polyamide polyamine epichlorohydrin is 11000D; the degree of deacetylation of chitosan is 85%, and the average molecular weight is 5000D.
PUM
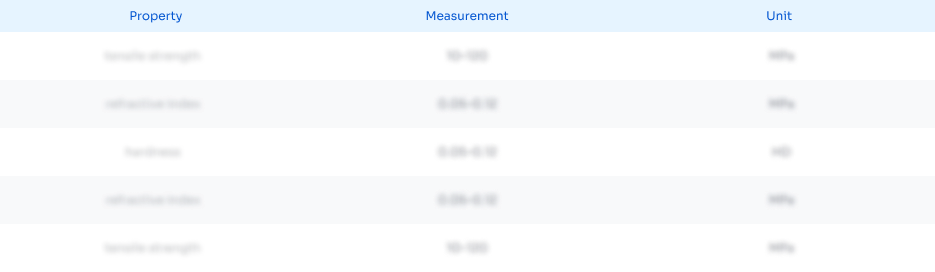
Abstract
Description
Claims
Application Information

- R&D Engineer
- R&D Manager
- IP Professional
- Industry Leading Data Capabilities
- Powerful AI technology
- Patent DNA Extraction
Browse by: Latest US Patents, China's latest patents, Technical Efficacy Thesaurus, Application Domain, Technology Topic, Popular Technical Reports.
© 2024 PatSnap. All rights reserved.Legal|Privacy policy|Modern Slavery Act Transparency Statement|Sitemap|About US| Contact US: help@patsnap.com