Medium temperature curing filler putty insulating material
An insulating material and putty technology, which is applied in the field of gap filling insulating materials, can solve the problems of low production efficiency, high energy consumption, and failure to meet the requirements of digital production lines, etc., to achieve high production efficiency, save production energy consumption, shorten time and increase efficiency The effect of technical requirements
- Summary
- Abstract
- Description
- Claims
- Application Information
AI Technical Summary
Problems solved by technology
Method used
Image
Examples
Embodiment Construction
[0028] Medium temperature curing putty insulation material, the formula is as follows: g
[0029] Epoxy resin E44 80
[0030] Epoxy resin E12 30
[0031] Tongmaic anhydride 30
[0032] imidazole 2
[0033] Mica powder 600 mesh 150
[0034] Clay 1000 mesh 50.
[0035] Its manufacturing method is as follows:
[0036] 1) According to the material formula, stir and mix epoxy resin E44 and epoxy resin E12 at 100°C, then lower it to 40°C; add tungalic anhydride to the obtained synthetic epoxy resin and stir evenly; raise the temperature to 60°C, continue to stir and observe the color change of the glue solution. After the glue solution is transparent, measure the gelation time at 170°C every 30 minutes, control the gelation time to 5 minutes or less, add imidazole, stop stirring and cool down to room temperature.
[0037] 2) Put mica powder and pottery clay in an electric oven at 120°C for baking and drying for more than 4 hours,
[0038] 3) Pour the above-mentioned synthetic...
PUM
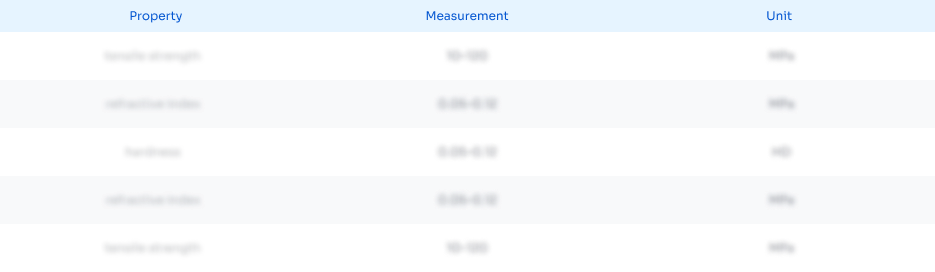
Abstract
Description
Claims
Application Information

- Generate Ideas
- Intellectual Property
- Life Sciences
- Materials
- Tech Scout
- Unparalleled Data Quality
- Higher Quality Content
- 60% Fewer Hallucinations
Browse by: Latest US Patents, China's latest patents, Technical Efficacy Thesaurus, Application Domain, Technology Topic, Popular Technical Reports.
© 2025 PatSnap. All rights reserved.Legal|Privacy policy|Modern Slavery Act Transparency Statement|Sitemap|About US| Contact US: help@patsnap.com