Injection mold adopting IMR process and application method for injection mold
An injection mold and process technology, applied in the field of IMR process injection mold, can solve the problems of low cost, not as wear-resistant as IMD, short injection molding cycle, etc., and achieve the effect of compact structure, elimination of curling, and reasonable structure design.
- Summary
- Abstract
- Description
- Claims
- Application Information
AI Technical Summary
Problems solved by technology
Method used
Image
Examples
Embodiment Construction
[0023] Figure 1-6 Shown is the relevant explanatory figure of the present invention; Figure 1-6 As shown, an IMR process injection mold:
[0024] The mold structure adopts a two-plate mold cold runner injection molding structure, and the layout is one mold with two cavities. The molded parts adopt the insert insert method, mainly including figure 1 The cavity insert 8 and the core insert 10 shown in the cross-section of A-A in the middle, in order to ensure the accuracy of the reset when the cavity insert 8 and the core insert 10 are opened and closed, a matching positioning feature between the two is specially designed Mo Ren Hukou 33.
[0025] The mold pouring system adopts the cold runner latent gate pouring method, such as Figure 5 As shown in the cross-sectional view of C-C, a single product adopts the double gate casting method, and the gate of the latent gate is designed on the gate thimble 26, and the gate diameter is The latent gate is beneficial to the autom...
PUM
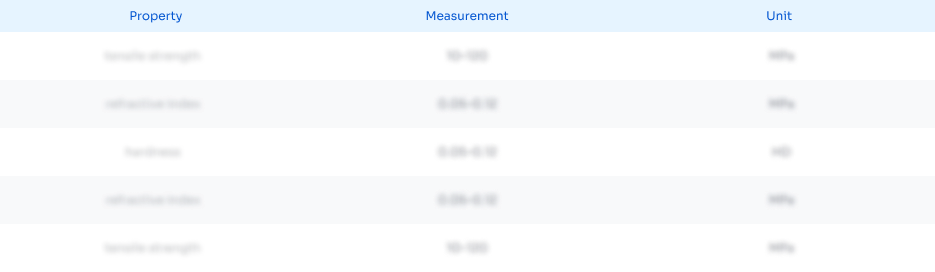
Abstract
Description
Claims
Application Information

- Generate Ideas
- Intellectual Property
- Life Sciences
- Materials
- Tech Scout
- Unparalleled Data Quality
- Higher Quality Content
- 60% Fewer Hallucinations
Browse by: Latest US Patents, China's latest patents, Technical Efficacy Thesaurus, Application Domain, Technology Topic, Popular Technical Reports.
© 2025 PatSnap. All rights reserved.Legal|Privacy policy|Modern Slavery Act Transparency Statement|Sitemap|About US| Contact US: help@patsnap.com