Preparation method of high thermal conductivity ceramic aluminum-based copper clad laminate
A technology of aluminum-based copper-clad laminates and high thermal conductivity ceramics, applied in chemical instruments and methods, non-polymer adhesive additives, lamination, etc., can solve problems such as increasing the thickness of ceramic aluminum-based copper-clad laminates and increasing production costs, and achieve Excellent thermal conductivity and insulation performance, reduced thickness, and improved economic benefits
- Summary
- Abstract
- Description
- Claims
- Application Information
AI Technical Summary
Problems solved by technology
Method used
Examples
Embodiment 1
[0011] Embodiment 1: The preparation method of high thermal conductivity ceramic aluminum-based copper-clad laminate, which includes the following steps: (1), aluminum plate pretreatment: evenly coat a layer of composite paint with a thickness of 2mm on the aluminum plate and dry it at 220 ° C, The composite coating includes by weight: 10 parts of neutral silicone glue, 4 parts of castor oil polyoxyethylene ether and 4 parts of sodium petroleum sulfonate; (2), ceramic treatment of aluminum plate: uniform ceramic enamel with a spray gun Spray it on the aluminum plate, and then strengthen it at 350°C for 20 minutes to form a vitrified aluminum plate. The ceramic enamel includes by weight: 2 parts of alumina, 28 parts of silicon dioxide, 7 parts of titanium dioxide, 6 parts of boron oxide and 3 parts of Microcrystalline cellulose, the thickness of the enamel spraying is 2 μm; (3), coating the bonding layer: coating the bonding layer on the surface of the ceramicized aluminum plate...
Embodiment 2
[0012] Embodiment 2: The preparation method of high thermal conductivity ceramic aluminum-based copper-clad laminate, which includes the following steps: (1), aluminum plate pretreatment: evenly coat a layer of composite paint with a thickness of 3mm on the aluminum plate and dry it at 230 ° C, The composite coating includes by weight: 15 parts of neutral silicone glue, 5 parts of castor oil polyoxyethylene ether and 6 parts of sodium petroleum sulfonate; (2), ceramic treatment of aluminum plate: uniform ceramic enamel with spray gun Spray it on the aluminum plate, and then strengthen it at 360°C for 25 minutes to form a vitrified aluminum plate. The ceramic enamel includes by weight: 3 parts of alumina, 30 parts of silicon dioxide, 8 parts of titanium dioxide, 7 parts of boron oxide and 4 parts Microcrystalline cellulose, the thickness of the enamel spraying is 5 μm; (3), coating the bonding layer: coating the bonding layer on the surface of the ceramized aluminum plate, the b...
Embodiment 3
[0013] Embodiment 3: The preparation method of high thermal conductivity ceramic aluminum-based copper-clad laminate, which includes the following steps: (1), aluminum plate pretreatment: evenly coat a layer of composite paint with a thickness of 4mm on the aluminum plate and dry it at 240 ° C, The composite coating includes by weight: 20 parts of neutral silicone glue, 6 parts of castor oil polyoxyethylene ether and 8 parts of sodium petroleum sulfonate; (2), ceramic treatment of aluminum plate: use a spray gun to uniformly coat the ceramic enamel Spray it on the aluminum plate, and then strengthen it at 370°C for 30 minutes to form a vitrified aluminum plate. The ceramic enamel includes by weight: 4 parts of alumina, 33 parts of silicon dioxide, 10 parts of titanium dioxide, 8 parts of boron oxide and 5 parts Microcrystalline cellulose, the thickness of the enamel spraying is 8 μm; (3), coating the bonding layer: coating the bonding layer on the surface of the ceramicized alu...
PUM
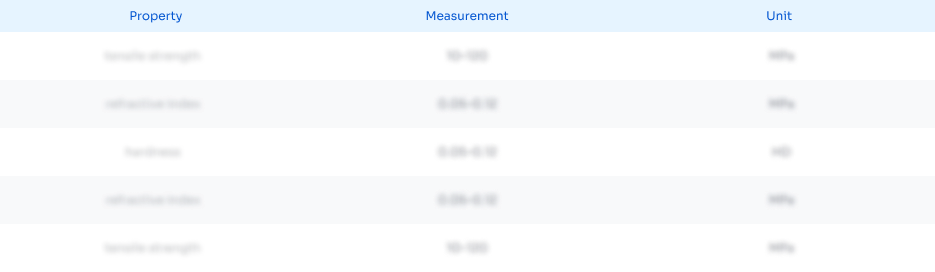
Abstract
Description
Claims
Application Information

- R&D Engineer
- R&D Manager
- IP Professional
- Industry Leading Data Capabilities
- Powerful AI technology
- Patent DNA Extraction
Browse by: Latest US Patents, China's latest patents, Technical Efficacy Thesaurus, Application Domain, Technology Topic, Popular Technical Reports.
© 2024 PatSnap. All rights reserved.Legal|Privacy policy|Modern Slavery Act Transparency Statement|Sitemap|About US| Contact US: help@patsnap.com