Press buckle type rock wool composite board and manufacturing method thereof
A manufacturing method and technology of composite panels, applied in chemical instruments and methods, synthetic resin layered products, building components, etc., can solve problems affecting human health, carcinogenicity, etc., and achieve significant fire prevention effects, reduced emission, and full response effects
- Summary
- Abstract
- Description
- Claims
- Application Information
AI Technical Summary
Problems solved by technology
Method used
Image
Examples
Embodiment 1
[0041] Such as Figure 1 to Figure 3 As shown, the buckle-type rock wool composite board of this embodiment includes a rock wool matrix layer 1, a reinforcement layer 2, a surface layer 3 and a buckle structure 4, and the reinforcement layer 2 is sandwiched between the rock wool matrix layers 1; the surface layer 3 is connected to the reinforcement layer 2 through the buckle structure 4, and the surface layer 3 is closely attached to the rock wool matrix layer 1.
[0042] Among them: the rock wool matrix layer 1 is made of basalt, blast furnace slag, fly ash, and waste rock wool blocks as raw materials, which are melted at high temperature, blown into fibers by high-speed centrifugal force or high-pressure gas, and are obtained by adding an appropriate amount of thermosetting resin adhesive and water-repellent agent. , the addition amount is 0.8-1% of the total mass, and its raw material is to increase the waste rock wool block, and the addition amount of the waste rock wool b...
Embodiment 2
[0047] The manufacturing method of the buckle type rock wool composite board of the present embodiment comprises the following specific steps:
[0048] Step S101, raw material preparation: mix 62% of blast furnace slag, 25% of basalt, 10% of fly ash, and 3% of waste rock wool block, wherein the particle size of basalt is 8cm, and the block diameter of waste rock wool block is 8cm , to feed the raw materials through the conveyor into the cupola to melt them into a liquid mixture;
[0049] Step S102, fiber preparation: the liquid mixture is continuously flowed into the high-speed rotating centrifugal rolls through the melt launder. Rotate, the upper and lower corresponding centrifugal rollers rotate in the same direction; the outer side of the centrifugal roller is surrounded by an air curtain formed by the blower, the liquid mixture is thrown four times by the centrifugal roller and condensed into silky fibers under the action of air cooling, the fiber filaments are After bein...
Embodiment 3
[0056] The manufacturing method of the buckle type rock wool composite board of the present embodiment comprises the following specific steps:
[0057] Step S101, raw material preparation: mix 62% of blast furnace slag, 22% of basalt, 13% of fly ash, and 3% of waste rock wool block, wherein the particle size of basalt is 8cm, and the block diameter of waste rock wool block is 8cm , to feed the raw materials through the conveyor into the cupola to melt them into a liquid mixture;
[0058] Step S102, fiber preparation: the liquid mixture is continuously flowed into the high-speed rotating centrifugal rolls through the melt launder. Rotate, the upper and lower corresponding centrifugal rollers rotate in the same direction; the outer side of the centrifugal roller is surrounded by an air curtain formed by the blower, the liquid mixture is thrown four times by the centrifugal roller and condensed into silky fibers under the action of air cooling, the fiber filaments are After bein...
PUM
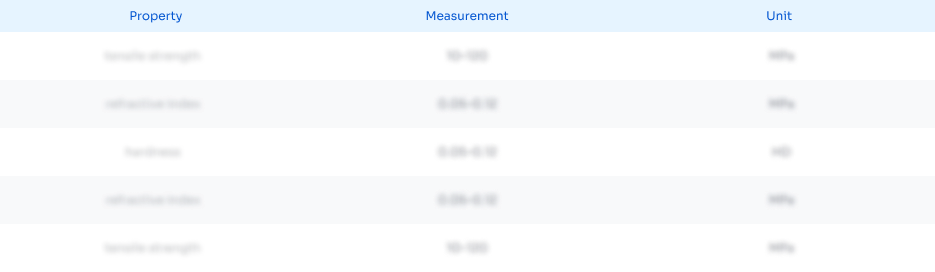
Abstract
Description
Claims
Application Information

- R&D
- Intellectual Property
- Life Sciences
- Materials
- Tech Scout
- Unparalleled Data Quality
- Higher Quality Content
- 60% Fewer Hallucinations
Browse by: Latest US Patents, China's latest patents, Technical Efficacy Thesaurus, Application Domain, Technology Topic, Popular Technical Reports.
© 2025 PatSnap. All rights reserved.Legal|Privacy policy|Modern Slavery Act Transparency Statement|Sitemap|About US| Contact US: help@patsnap.com