Method for preparing graphene by taking coal as raw material
A graphene and raw material technology, which is applied in the field of graphene preparation using microwave pyrolysis technology and supercritical carbon dioxide technology, can solve the problems of uneven distribution and high preparation cost, and achieves a reduced production cost, low raw material cost and regular crystal structure. Effect
- Summary
- Abstract
- Description
- Claims
- Application Information
AI Technical Summary
Problems solved by technology
Method used
Image
Examples
Embodiment 1
[0039] The present embodiment 1 is tested with lignite as raw material.
[0040] (1) Evenly mix 50g of lignite powder with particle size less than 0.221mm, 10g of kaolinite and 10g of sodium carbonate, and dry in a vacuum drying oven;
[0041] (2) Place the dried sample in a microwave pyrolysis reactor, set the microwave power of the reactor to 400W, the final temperature to 400°C, and the reaction time to 15min, then continue to heat up to 1000°C, and the microwave power to 1000W, The reaction time is 10 minutes;
[0042] (3) After the reaction, cool the reactor to room temperature, take out the reaction material, wash it with 0.1mol / L potassium permanganate cleaning solution, dry it, and then clean it again in an ultrasonic cleaner with an ultrasonic frequency of 30KHz and a power of It was 130W, and the ultrasonic cleaning time was 15min, and sample A was obtained;
[0043] (4) Mix the sample A and the dispersant sodium alkylbenzene sulfonate at a mass ratio of 2:1, put t...
Embodiment 2
[0046] In Example 2, long-flame coal was used as the raw material for testing.
[0047] (1) After uniformly mixing 50g of long-flame coal powder with a particle size of less than 0.221mm, 10g of kaolinite and 10g of sodium carbonate, place it in a vacuum drying oven to dry;
[0048] (2) Place the dried sample in a microwave pyrolysis reactor, set the microwave power of the reactor to 400W, the final temperature to 400°C, and the reaction time to 15min, then continue to heat up to 1000°C, and the microwave power to 1000W, The reaction time is 10 minutes;
[0049] (3) After the reaction, cool the reactor to room temperature, take out the reaction material, wash it with 0.1mol / L potassium permanganate cleaning solution, dry it, and then clean it again in an ultrasonic cleaner with an ultrasonic frequency of 30KHz and a power of It was 130W, and the ultrasonic cleaning time was 15min, and sample A was obtained;
[0050] (4) Mix the sample A and the dispersant sodium alkylbenzene...
Embodiment 3
[0053] In Example 3, the mixed sample of lignite and long-flame coal is used as raw material
[0054] (1) After uniformly mixing 25g of lignite powder with a particle size of less than 0.221mm, 25g of long-flame coal powder, 10g of kaolinite and 10g of sodium carbonate, place it in a vacuum drying oven to dry;
[0055] (2) Place the dried sample in a microwave pyrolysis reactor, set the microwave power of the reactor to 400W, the final temperature to 400°C, and the reaction time to 15min, then continue to heat up to 1000°C, and the microwave power to 1000W, The reaction time is 10 minutes;
[0056] (3) After the reaction, cool the reactor to room temperature, take out the reaction material, wash it with 0.1mol / L potassium permanganate cleaning solution, dry it, and then clean it again in an ultrasonic cleaner with an ultrasonic frequency of 30KHz and a power of It was 130W, and the ultrasonic cleaning time was 15min, and sample A was obtained;
[0057] (4) Mix the sample A a...
PUM
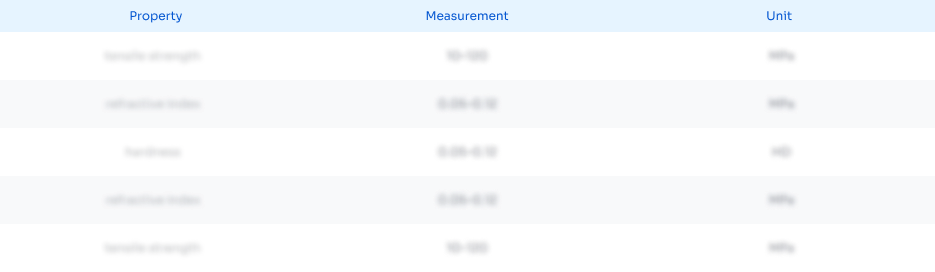
Abstract
Description
Claims
Application Information

- Generate Ideas
- Intellectual Property
- Life Sciences
- Materials
- Tech Scout
- Unparalleled Data Quality
- Higher Quality Content
- 60% Fewer Hallucinations
Browse by: Latest US Patents, China's latest patents, Technical Efficacy Thesaurus, Application Domain, Technology Topic, Popular Technical Reports.
© 2025 PatSnap. All rights reserved.Legal|Privacy policy|Modern Slavery Act Transparency Statement|Sitemap|About US| Contact US: help@patsnap.com