Double-station robot automatic welding system
An automatic welding, dual-station technology, applied in welding equipment, auxiliary welding equipment, welding/cutting auxiliary equipment, etc., can solve problems such as harming the physical and mental health of workshop workers, inability to realize automatic production, and impact on welding positioning accuracy, and achieve a reduction in Injury to workers, effects of high equipment production efficiency and high degree of automation
- Summary
- Abstract
- Description
- Claims
- Application Information
AI Technical Summary
Problems solved by technology
Method used
Image
Examples
Embodiment Construction
[0026] The present invention will be further described below in conjunction with accompanying drawing and specific embodiment:
[0027] Such as figure 1 , figure 2 with image 3 As shown, the present invention includes a fixed feed bin 100, a loading and unloading robot system 200, a double-station welding workbench 300, a welding robot system 400, a control system 500, and a welding room 600; the fixed feed bin 100 is used to store workpieces to be processed and Workpieces, loading and unloading robot system 200 is used to transport the workpieces to be processed and the workpieces between the fixed silo 100 and the double-station welding workbench 300; the workpieces to be processed in this example are sheet metal boxes; the double-station The welding workbench 300 is set between the loading and unloading robot system 200 and the welding room 600 , the double-station welding workbench 300 can rotate horizontally, and the welding robot system 400 and the control system 500...
PUM
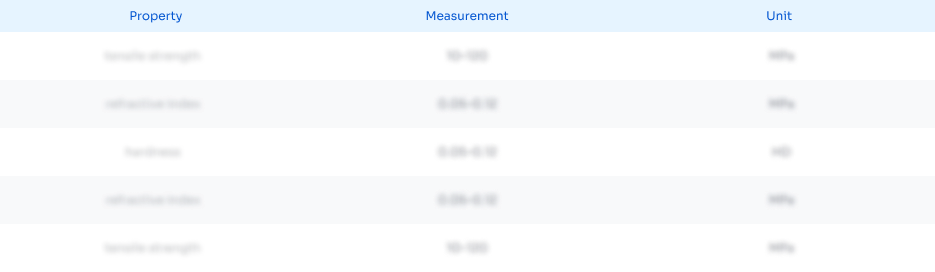
Abstract
Description
Claims
Application Information

- Generate Ideas
- Intellectual Property
- Life Sciences
- Materials
- Tech Scout
- Unparalleled Data Quality
- Higher Quality Content
- 60% Fewer Hallucinations
Browse by: Latest US Patents, China's latest patents, Technical Efficacy Thesaurus, Application Domain, Technology Topic, Popular Technical Reports.
© 2025 PatSnap. All rights reserved.Legal|Privacy policy|Modern Slavery Act Transparency Statement|Sitemap|About US| Contact US: help@patsnap.com