A cross-spinning strengthening method for magnesium alloy thin-walled cylindrical parts
A magnesium alloy, thin-walled cylinder technology, applied in metal processing equipment, forming tools, manufacturing tools, etc., can solve the problems of low circumferential tensile strength and low axial tensile strength of magnesium alloy thin-walled cylindrical parts, and achieve the The effects of improved radial and radial mechanical properties, uniform microstructure distribution, and reduced anisotropy
- Summary
- Abstract
- Description
- Claims
- Application Information
AI Technical Summary
Problems solved by technology
Method used
Image
Examples
specific Embodiment approach 1
[0026] Specific Embodiment 1: In this embodiment, a cross-spinning strengthening method for magnesium alloy thin-walled cylindrical parts is carried out according to the following steps:
[0027] Step 1: Put the magnesium alloy billet on the mandrel of the spinning machine and fix it, preheat the mandrel of the spinning machine and the magnesium alloy billet, and then uniformly coat the outer surface of the mandrel of the spinning machine and the outer surface of the magnesium alloy billet spray lubricant;
[0028] Step 2: preheating the mandrel of the spinning machine, the wheel of the spinning machine and the magnesium alloy blank to the spinning temperature;
[0029] The spinning temperature of the mandrel of the spinning machine and the magnesium alloy blank is 200-450°C; the spinning temperature of the spinning wheel of the spinning machine is 100-150°C;
[0030] Step 3: Start the spinning machine for strong spinning;
[0031] Step 4: Change the rotation direction of th...
specific Embodiment approach 2
[0034] Embodiment 2: This embodiment differs from Embodiment 1 in that: in Step 1, the mandrel of the spinning machine is preheated to 150°C. Others are the same as in the first embodiment.
specific Embodiment approach 3
[0035] Embodiment 3: The difference between this embodiment and Embodiment 1 or 2 is that the magnesium alloy billet is preheated to 150° C. in Step 1. Others are the same as in the first or second embodiment.
PUM
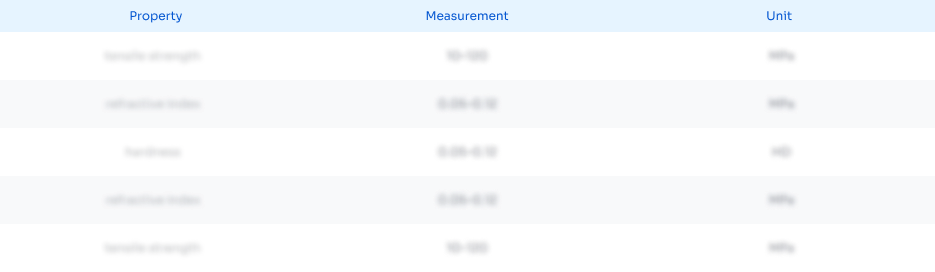
Abstract
Description
Claims
Application Information

- R&D
- Intellectual Property
- Life Sciences
- Materials
- Tech Scout
- Unparalleled Data Quality
- Higher Quality Content
- 60% Fewer Hallucinations
Browse by: Latest US Patents, China's latest patents, Technical Efficacy Thesaurus, Application Domain, Technology Topic, Popular Technical Reports.
© 2025 PatSnap. All rights reserved.Legal|Privacy policy|Modern Slavery Act Transparency Statement|Sitemap|About US| Contact US: help@patsnap.com