High-hardness oil spray nozzle and manufacturing method thereof
A manufacturing method and technology of fuel injection nozzles, which are applied in the direction of manufacturing tools, fuel injection devices, furnace types, etc., can solve the problems of low hardness and poor wear resistance, achieve long working life, improve mechanical properties, and prevent thermal cracking trends. Effect
- Summary
- Abstract
- Description
- Claims
- Application Information
AI Technical Summary
Problems solved by technology
Method used
Examples
Embodiment Construction
[0020] The present invention will be further described below:
[0021] High-hardness fuel injector, the composition of the fuel injector by mass percentage is as follows: C 0.7~2.11%, Cr 15~25%, Mo0.5~1.7%, Si ≤0.08%, Ni 0.05~0.2%, Mn 0.07~ 1.02%, P ≤0.08%, S ≤0.06%, and the balance is Fe.
[0022] A high-hardness fuel injector and its manufacturing method, comprising the following steps:
[0023] (1) Material preparation: Prepare materials according to the following weight percentages: C 0.7%, Cr 15%, Mo 0.5%, Si ≤0.08%, Ni0.05%, Mn 0.07%, P ≤0.08%, S ≤0.06%, and the rest The amount is Fe;
[0024] (2) After the above raw materials are melted;
[0025] (3) After it is completely melted, add it to the medium, then add manganese and silicon for deoxidation, take samples to adjust the composition to the requirements, and the molten iron enters the pouring process at 1500-1530 °C;
[0026] (4) In the pouring process, the castings are immediately cooled by heat preservation af...
PUM
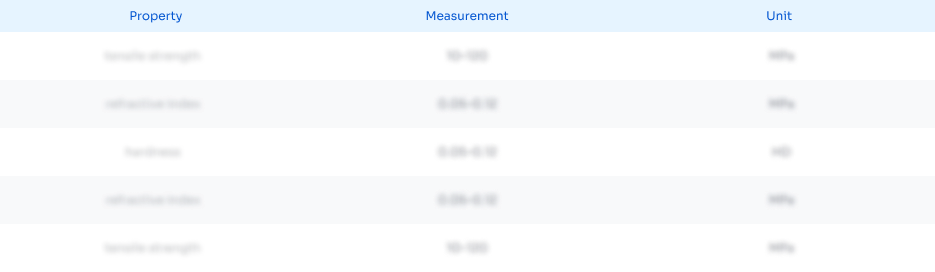
Abstract
Description
Claims
Application Information

- R&D
- Intellectual Property
- Life Sciences
- Materials
- Tech Scout
- Unparalleled Data Quality
- Higher Quality Content
- 60% Fewer Hallucinations
Browse by: Latest US Patents, China's latest patents, Technical Efficacy Thesaurus, Application Domain, Technology Topic, Popular Technical Reports.
© 2025 PatSnap. All rights reserved.Legal|Privacy policy|Modern Slavery Act Transparency Statement|Sitemap|About US| Contact US: help@patsnap.com