Drying and pelletizing device for chemical engineering
A drying system and chemical technology, applied in the field of chemical drying and granulation equipment, can solve the problems of uneven heating, low drying efficiency, waste of energy, etc., to increase the heat exchange surface area, increase the contact area, increase The effect of heat transfer efficiency
- Summary
- Abstract
- Description
- Claims
- Application Information
AI Technical Summary
Problems solved by technology
Method used
Image
Examples
Embodiment Construction
[0019] The present invention will be further described below with reference to the accompanying drawings and embodiments, and the mode of the present invention includes but not limited to the following embodiments.
[0020] The purpose of this embodiment is to provide a material drying device with simple structure, reasonable design, good drying effect and high drying efficiency, such as figure 1 As shown, the drying device mainly includes two support bases 1, a drum 2, a steam coil 3, a motor 4 and a material classification device.
[0021] Specifically, two ends of the drum 2 are fixedly provided with a connecting end 21, and the two connecting ends are respectively connected to the two supporting bases 1 through rotating bearings; the steam coil 3 is a spiral steam coil, The steam coil is close to the inner wall of the drum and is spirally arranged along the axis of the drum. The two ends of the steam coil 3 are respectively connected with a steam inlet pipe 31 and a steam ...
PUM
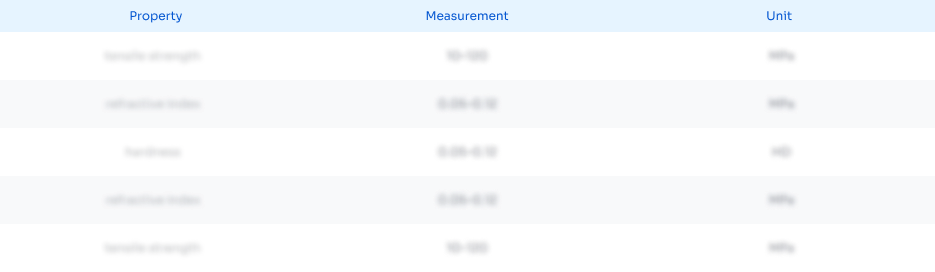
Abstract
Description
Claims
Application Information

- R&D
- Intellectual Property
- Life Sciences
- Materials
- Tech Scout
- Unparalleled Data Quality
- Higher Quality Content
- 60% Fewer Hallucinations
Browse by: Latest US Patents, China's latest patents, Technical Efficacy Thesaurus, Application Domain, Technology Topic, Popular Technical Reports.
© 2025 PatSnap. All rights reserved.Legal|Privacy policy|Modern Slavery Act Transparency Statement|Sitemap|About US| Contact US: help@patsnap.com