Cartap workshop exhaust gas treatment method
A workshop exhaust gas and treatment method technology, applied in the direction of gas treatment, separation methods, chemical instruments and methods, etc., can solve the problems of thorough absorption and purification of non-volatile organic matter, and achieve the goal of simplifying the exhaust gas treatment process, reducing labor operations, and reducing pollution Effect
- Summary
- Abstract
- Description
- Claims
- Application Information
AI Technical Summary
Problems solved by technology
Method used
Image
Examples
Embodiment 1
[0036] A method for treating waste gas in a cartap workshop:
[0037] Technical problem to be solved by the present invention adopts following technical scheme to realize:
[0038] (1) Tail gas containing dichloroethane is first washed with 2-stage alkali, then washed with water, demisted, pre-treated, and then treated with 3 boxes of 6-core 2-stage activated carbon fiber treatment devices; finally, the exhaust gas is combined into photocatalysis Oxidation device;
[0039] (2) The comprehensive tail gas is first treated with an alkali washing tower, then a water absorption tower, and then 3 boxes of 2-stage activated carbon particle adsorption equipment for treatment;
[0040] (3) Allyl chloride is first condensed with cold brine, and then the equipment is comprehensively treated; finally, the exhaust gas enters the photocatalytic oxidation device;
[0041] (4) Dimethylamine and allylamine tail gas are first treated with original acid absorption equipment, then water washing...
Embodiment 2
[0060] A method for treating waste gas in a cartap workshop:
[0061] Technical problem to be solved by the present invention adopts following technical scheme to realize:
[0062] (1) Tail gas containing dichloroethane is first washed with 2-stage alkali, then washed with water, demisted, pre-treated, and then treated with 3 boxes of 6-core 2-stage activated carbon fiber treatment devices; finally, the exhaust gas is combined into photocatalysis Oxidation device;
[0063] (2) The comprehensive tail gas is first treated with an alkali washing tower, then a water absorption tower, and then 3 boxes of 2-stage activated carbon particle adsorption equipment for treatment;
[0064] (3) Allyl chloride is first condensed with cold brine, and then the equipment is comprehensively treated; finally, the exhaust gas enters the photocatalytic oxidation device;
[0065] (4) Dimethylamine and allylamine tail gas are first treated with original acid absorption equipment, then water washing...
PUM
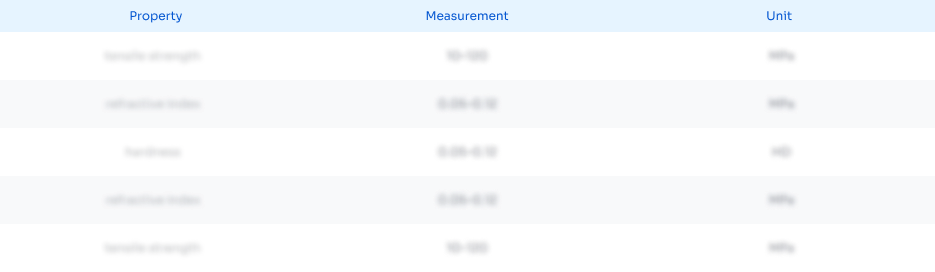
Abstract
Description
Claims
Application Information

- R&D Engineer
- R&D Manager
- IP Professional
- Industry Leading Data Capabilities
- Powerful AI technology
- Patent DNA Extraction
Browse by: Latest US Patents, China's latest patents, Technical Efficacy Thesaurus, Application Domain, Technology Topic, Popular Technical Reports.
© 2024 PatSnap. All rights reserved.Legal|Privacy policy|Modern Slavery Act Transparency Statement|Sitemap|About US| Contact US: help@patsnap.com