A method for direct continuous casting of molten iron into billets
A technology of continuous casting of molten iron, which is applied in the field of direct continuous casting of steel billets without the molten iron passing through the converter or electric furnace, so as to achieve the effects of reducing the process, ensuring continuity and saving production time
- Summary
- Abstract
- Description
- Claims
- Application Information
AI Technical Summary
Problems solved by technology
Method used
Image
Examples
Embodiment 1
[0029] [Example 1] Taking the smelting of Q235B steel as an example;
[0030] 1) The temperature of the molten iron is 1480°C. In the first U-shaped tank 3, the molten iron is desulfurized to a sulfur content of 0.010% by Ca-Mg composite desulfurization;
[0031] 2) After desulfurization, the molten iron passes through the sealed iron trough 6, and blows oxygen through the oxygen lance 7 so that the FeO content in the molten iron reaches 18%;
[0032] 3) In the second U-shaped groove 10, the composite slagging material of active lime+fluorite+light-burned dolomite is sprayed through the spray gun 9, and the weight ratio of each component is active lime: fluorite: light-burned dolomite=15: 1:6, the main chemical composition of tapping is: carbon 0.11%, phosphorus 0.015%, sulfur 0.009%, tapping temperature 1665°C;
[0033] 4) Carry out alloying treatment on the molten steel at the tap hole 11, the components of the treated molten steel are C: 0.16%; Si: 0.080%; Mn: 0.27%; P: 0....
Embodiment 2
[0035] [Example 2] Taking the smelted SPHC steel grade as an example;
[0036] 1) The temperature of the molten iron is 1500°C. In the first U-shaped tank 3, the molten iron is desulfurized to a sulfur content of 0.005% by Ca-Mg composite desulfurization;
[0037] 2) After desulfurization, the molten iron passes through the sealed iron trough 6, and blows oxygen through the oxygen lance 7 so that the FeO content in the molten iron reaches 20%;
[0038] 3) In the second U-shaped groove 10, the composite slagging material of active lime+fluorite+light-burned dolomite is sprayed through the spray gun 9, and the weight ratio of each component is active lime: fluorite: light-burned dolomite=15 :1:6, the main chemical composition of tapping is: carbon 0.05%, phosphorus 0.013%, sulfur 0.007%, tapping temperature 1670°C;
[0039] 4) Carry out alloying treatment on the molten steel at the tap hole 11, the composition of the treated molten steel is C: 0.06%; Si: 0.007%: Mn: 0.21%: P: 0...
PUM
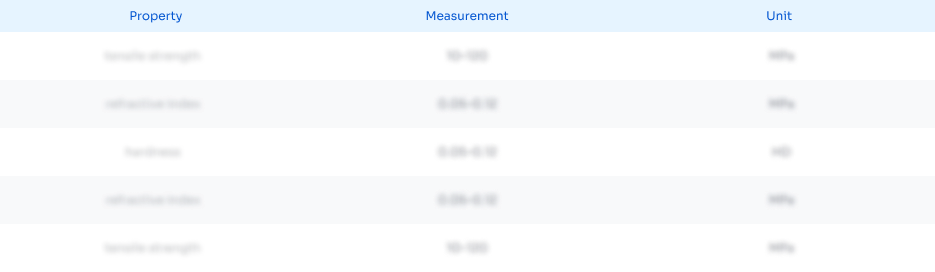
Abstract
Description
Claims
Application Information

- R&D Engineer
- R&D Manager
- IP Professional
- Industry Leading Data Capabilities
- Powerful AI technology
- Patent DNA Extraction
Browse by: Latest US Patents, China's latest patents, Technical Efficacy Thesaurus, Application Domain, Technology Topic, Popular Technical Reports.
© 2024 PatSnap. All rights reserved.Legal|Privacy policy|Modern Slavery Act Transparency Statement|Sitemap|About US| Contact US: help@patsnap.com