Wet desulphurization smoke dewatering reheating and afterheat using ultra-low emission system and method
A wet desulfurization and emission system technology, applied in combustion methods, emission prevention, greenhouse gas reduction, etc., can solve problems such as unfavorable thermal power plant operation economy and energy utilization, unavailability of waste heat, difficult diffusion of pollutants, etc. The effect of spraying circulating water, reducing energy consumption, and saving energy in system operation
- Summary
- Abstract
- Description
- Claims
- Application Information
AI Technical Summary
Problems solved by technology
Method used
Image
Examples
Embodiment 1
[0158] Machine assembly capacity: 330MW unit;
[0159] Total flue gas: 110×10 4 Nm 3 / h(396kg / s);
[0160] Exhaust temperature before desulfurization: 153℃;
[0161] Such as figure 1 As shown, the 145°C flue gas is passed into the flue gas cooler 1 to recover the sensible heat in the flue gas, and the temperature of the flue gas is reduced to 85°C; the 57°C water in the water circulation pipeline system is heated to 88°C.
[0162] The flue gas enters the desulfurization tower 2 for desulfurization treatment. After the desulfurization treatment is completed, the temperature of the flue gas is 55°C; the volume content of moisture in the desulfurization flue gas is 15.97% (mass fraction 10%);
[0163] The flue gas along the pipeline enters the first-level spray tower 3 from the top of the first-level spray tower 3. After the first spray treatment, the temperature of the flue gas drops to 43°C;
[0164] After the flue gas enters the secondary spray tower 4 along the pipeline, after the secon...
Embodiment 2
[0169] Machine assembly capacity: 330MW unit;
[0170] Total flue gas: 110×10 4 Nm 3 / h(396kg / s);
[0171] Exhaust temperature before desulfurization: 150℃;
[0172] Such as figure 1 As shown, the flue gas of 150°C is passed into the flue gas cooler 1 to recover the sensible heat in the flue gas, and the temperature of the flue gas is reduced to 90°C; the 60°C water in the water circulation pipeline system is heated to 90°C.
[0173] The flue gas enters the desulfurization tower 2 for desulfurization treatment. After the desulfurization treatment is completed, the temperature of the flue gas is 55°C; the volume content of moisture in the desulfurization flue gas is 15.97% (mass fraction 10%);
[0174] The flue gas along the pipeline enters the first-level spray tower 3 from the top of the first-level spray tower 3. After the first spray treatment, the temperature of the flue gas drops to 43°C;
[0175] After that, the flue gas enters the secondary spray tower 4 along the pipeline, and af...
PUM
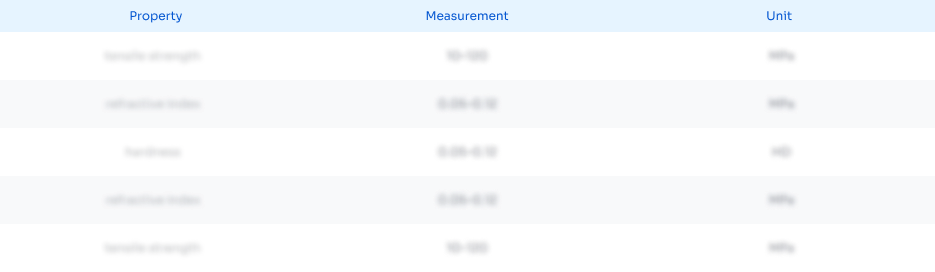
Abstract
Description
Claims
Application Information

- R&D Engineer
- R&D Manager
- IP Professional
- Industry Leading Data Capabilities
- Powerful AI technology
- Patent DNA Extraction
Browse by: Latest US Patents, China's latest patents, Technical Efficacy Thesaurus, Application Domain, Technology Topic, Popular Technical Reports.
© 2024 PatSnap. All rights reserved.Legal|Privacy policy|Modern Slavery Act Transparency Statement|Sitemap|About US| Contact US: help@patsnap.com