Processing method of nitride ceramic glaze
A technology of nitride ceramics and processing methods, which is applied in the field of ceramic processing, can solve the problems of inability to improve the wear resistance of ceramic products and lack of hardness, achieve good elasticity and wear resistance, and solve the problems of non-wear resistance and good melting performance Effect
- Summary
- Abstract
- Description
- Claims
- Application Information
AI Technical Summary
Problems solved by technology
Method used
Examples
Embodiment 1
[0012] The raw materials of the nitride ceramic glaze include a base material and an anti-wear agent, wherein the base material components and their mass parts are: 17 parts of limestone, 15 parts of kaolin, 25 parts of silicon nitride, 24 parts of calcium carbonate, 13 parts of zirconia, 18 parts of aluminum nitride; the anti-wear agent composition and its mass parts are: 5 parts of borax, 11 parts of mica, 15 parts of potassium feldspar, and 21 parts of quartz.
[0013] The preparation method of nitride ceramic glaze comprises the following steps:
[0014] (1) Limestone, kaolin, silicon nitride, calcium carbonate, zirconia, and aluminum nitride are prepared according to the ratio, and ground into powder;
[0015] (2) borax, mica, potassium feldspar, and quartz are prepared according to the ratio, and ground into powder;
[0016] (3) Mix the prepared base material with the anti-wear agent, then perform wet ball milling, and sieve the milled slurry to remove impurities to mak...
Embodiment 2
[0019] The raw materials of the nitride ceramic glaze include a base material and an anti-wear agent, wherein the base material components and their mass parts are: 19 parts of limestone, 18 parts of kaolin, 27 parts of silicon nitride, 22 parts of calcium carbonate, 10 parts of zirconia, 16 parts of aluminum nitride; the anti-wear agent composition and its mass parts are: 7 parts of borax, 14 parts of mica, 12 parts of potassium feldspar, and 18 parts of quartz.
[0020] The preparation method of nitride ceramic glaze comprises the following steps:
[0021] (1) Limestone, kaolin, silicon nitride, calcium carbonate, zirconia, and aluminum nitride are prepared according to the ratio, and ground into powder;
[0022] (2) borax, mica, potassium feldspar, and quartz are prepared according to the ratio, and ground into powder;
[0023] (3) Mix the prepared base material with the anti-wear agent, then perform wet ball milling, and sieve the milled slurry to remove impurities to mak...
Embodiment 3
[0026] The raw materials of the nitride ceramic glaze include a base material and an anti-wear agent, wherein the base material components and their mass parts are: 25 parts of limestone, 20 parts of kaolin, 32 parts of silicon nitride, 15 parts of calcium carbonate, 8 parts of zirconia, 13 parts of aluminum nitride; the anti-wear agent composition and its mass parts are: 9 parts of borax, 15 parts of mica, 9 parts of potassium feldspar, and 15 parts of quartz.
[0027] The preparation method of nitride ceramic glaze comprises the following steps:
[0028] (1) Limestone, kaolin, silicon nitride, calcium carbonate, zirconia, and aluminum nitride are prepared according to the ratio, and ground into powder;
[0029] (2) borax, mica, potassium feldspar, and quartz are prepared according to the ratio, and ground into powder;
[0030] (3) Mix the prepared base material with the anti-wear agent, then perform wet ball milling, and sieve the milled slurry to remove impurities to make ...
PUM
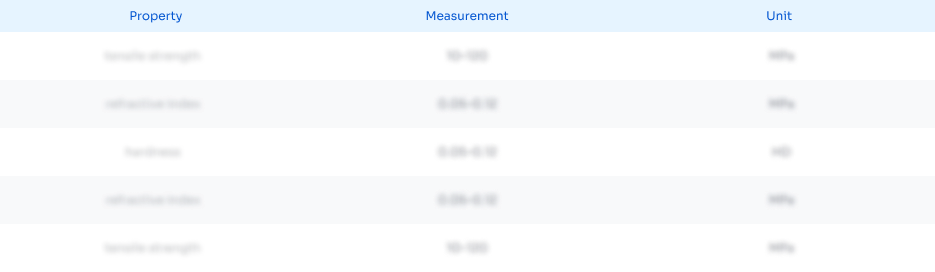
Abstract
Description
Claims
Application Information

- R&D
- Intellectual Property
- Life Sciences
- Materials
- Tech Scout
- Unparalleled Data Quality
- Higher Quality Content
- 60% Fewer Hallucinations
Browse by: Latest US Patents, China's latest patents, Technical Efficacy Thesaurus, Application Domain, Technology Topic, Popular Technical Reports.
© 2025 PatSnap. All rights reserved.Legal|Privacy policy|Modern Slavery Act Transparency Statement|Sitemap|About US| Contact US: help@patsnap.com