Coating modification one-step in-situ synthesis method of calcium phosphate-based composition anti-corrosion pigment
An anti-corrosion pigment, calcium phosphate technology, applied in the field of environmental chemistry, can solve the problems of poor dispersibility of calcium phosphate particles and can not protect metal materials well, and achieves inhibition of crystal growth, reduction of production costs, and good compatibility. Effect
- Summary
- Abstract
- Description
- Claims
- Application Information
AI Technical Summary
Problems solved by technology
Method used
Examples
Embodiment 1
[0021] According to the mass ratio of calcium phosphate to benzotriazole of 10:1, weigh 5.3 g of sodium phosphate, 1.0 g of benzotriazole, and 0.2 g of polyethylene glycol surfactant and disperse them in 100 mL of deionized water , to form dispersion system A; weigh 5.3 g of calcium nitrate and disperse it in 100 mL of deionized water to form dispersion system B. The reactor containing the dispersion system A was placed in an ultrasonic disperser, and the frequency of the ultrasonic wave was set to 100 kHz. Slowly add the above system B into system A dropwise, and keep stirring at a speed of 600 r / min. After the dropwise addition, take out the reaction vessel from the ultrasonic disperser, and let it stand and age at room temperature for 2 h. . The precipitate was filtered, washed with deionized water, dried in an oven at 95 °C for 2 h, and ground to obtain a calcium phosphate-based composite anticorrosion pigment. The anti-corrosion pigment is added to the paint to make a p...
Embodiment 2
[0023] According to the mass ratio of calcium phosphate to benzotriazole of 20:1, 10.6 g of sodium phosphate, 1.0 g of benzotriazole, and 0.3 Tween surfactant were respectively weighed and dispersed in 100 mL of deionized water to form Dispersion system A; Weigh 10.6 g of calcium nitrate and disperse it in 100 mL of deionized water to form dispersion system B. The reactor containing the dispersion system A was placed in an ultrasonic disperser, and the frequency of the ultrasonic wave was set to 100 kHz. Slowly add the above system B into system A dropwise, and keep stirring at a speed of 600 r / min. After the dropwise addition, take out the reaction vessel from the ultrasonic disperser, and let it stand and age at room temperature for 2 h. . The precipitate was filtered, washed with deionized water, dried in an oven at 95 °C for 2 h, and ground to obtain a calcium phosphate-based composite anticorrosion pigment. The anti-corrosion pigment is added to the paint to make a pain...
Embodiment 3
[0025] According to the mass ratio of calcium phosphate to benzotriazole of 30:1, weigh 15.9 g of sodium phosphate, 1 g of benzotriazole, and 0.4 g of triton x-100 surfactant and disperse them in 100 mL of Dispersion system A was formed in deionized water; 15.9 g of calcium nitrate was weighed and dispersed in 100 mL of deionized water to form dispersion system B. The reactor containing the dispersion system A was placed in an ultrasonic disperser, and the frequency of the ultrasonic wave was set to 100 kHz. Slowly add the above system B into system A dropwise, and keep stirring at a speed of 600 r / min. After the dropwise addition, take the reaction vessel out of the ultrasonic disperser, and let it stand and age for 5 h at room temperature. . The precipitate was filtered, washed with deionized water, dried in an oven at 95 °C for 2 h, and ground to obtain a calcium phosphate-based composite anticorrosion pigment. The anti-corrosion pigment is added to the paint to make a pa...
PUM
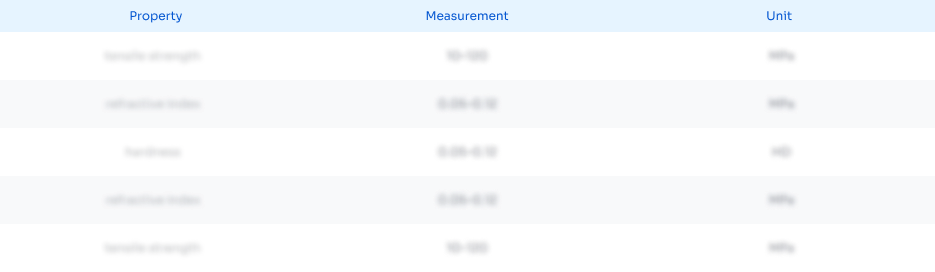
Abstract
Description
Claims
Application Information

- Generate Ideas
- Intellectual Property
- Life Sciences
- Materials
- Tech Scout
- Unparalleled Data Quality
- Higher Quality Content
- 60% Fewer Hallucinations
Browse by: Latest US Patents, China's latest patents, Technical Efficacy Thesaurus, Application Domain, Technology Topic, Popular Technical Reports.
© 2025 PatSnap. All rights reserved.Legal|Privacy policy|Modern Slavery Act Transparency Statement|Sitemap|About US| Contact US: help@patsnap.com