Novel route for preparing graphene using ethanol as liquid phase by planetary ball mill wet method
A planetary ball mill, graphene technology, applied in the direction of graphene, nano-carbon, etc., can solve the problems of low efficiency, poor controllability of the tape tearing method, and hindering the application of graphene.
- Summary
- Abstract
- Description
- Claims
- Application Information
AI Technical Summary
Problems solved by technology
Method used
Image
Examples
Embodiment 1
[0013] 1. Weigh 5g of graphite and place it in a ceramic jar, and after calcining in a muffle furnace at 300°C for 2 hours, place the calcined expanded graphite in a brown glass vessel for substitution;
[0014] 2. Weigh 0.5g of expanded graphite, put it in a beaker, then pour 20ml of ethanol organic solution into the beaker, and stir it ultrasonically for 60min before use; control the molar ratio of graphite to ethanol to be 1:4;
[0015] 3. Pour the above liquid into the agate jar, shake it to a uniform state, then put the agate jar on the planetary ball mill, after 500 rpm / min and 3h, pour out the liquid in the agate jar, and centrifuge with deionized water Graphene can be obtained after taking the supernatant and freeze-drying for 24 hours.
Embodiment 2
[0017] 1. Weigh 3g of graphite and place it in a ceramic jar, and after calcining in a muffle furnace at 290°C for 2.5 hours, place the calcined expanded graphite in a brown glass vessel for substitution;
[0018] 2. Weigh 0.6g of expanded graphite, put it in a beaker, then pour 25ml of ethanol organic solution into the beaker, and stir it ultrasonically for 50min before use; control the molar ratio of graphite to ethanol to be 1:4;
[0019] 3. Pour the above liquid into the agate jar, shake it to a uniform state, then put the agate jar on the planetary ball mill, after 600 rpm / min and 2.5h, pour out the liquid in the agate jar, and centrifuge with deionized water Afterwards, the supernatant was freeze-dried for 24 hours to obtain graphene.
Embodiment 3
[0021] 1. Weigh 3.5g of graphite and place it in a ceramic jar, and after calcining in a muffle furnace at 310°C for 1.5h, place the calcined expanded graphite in a brown glass vessel for substitution;
[0022] 2. Weigh 0.35g of expanded graphite, put it in a beaker, then pour 18ml of ethanol organic solution into the beaker, and stir it ultrasonically for 40min before use; control the molar ratio of graphite to ethanol to be 1:4;
[0023] 3. Pour the above liquid into the agate jar, shake it to a uniform state, then put the agate jar on the planetary ball mill, after 450 rpm / min and 3.5h, pour out the liquid in the agate jar, and centrifuge with deionized water Afterwards, the supernatant was freeze-dried for 24 hours to obtain graphene.
PUM
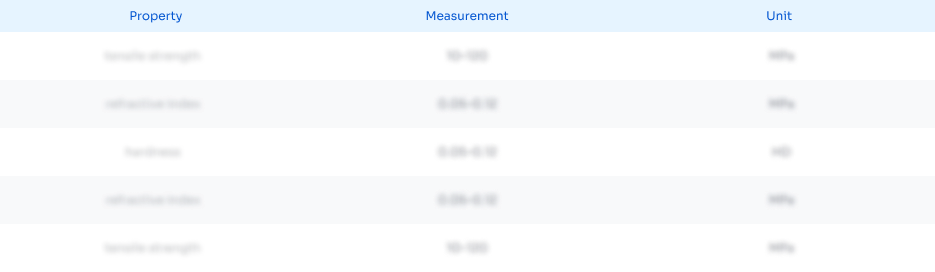
Abstract
Description
Claims
Application Information

- R&D
- Intellectual Property
- Life Sciences
- Materials
- Tech Scout
- Unparalleled Data Quality
- Higher Quality Content
- 60% Fewer Hallucinations
Browse by: Latest US Patents, China's latest patents, Technical Efficacy Thesaurus, Application Domain, Technology Topic, Popular Technical Reports.
© 2025 PatSnap. All rights reserved.Legal|Privacy policy|Modern Slavery Act Transparency Statement|Sitemap|About US| Contact US: help@patsnap.com