Precision mold for multiple times of injection of single melt
A technology of multiple injections and precision molds, applied in the field of injection molding molds, rubber and plastic injection molding molds, can solve problems such as difficulty in adapting to small batch production, high mold cost, long manufacturing cycle, etc., to achieve precision and automatic control, Save equipment and mold costs and achieve the effect of precise size control
- Summary
- Abstract
- Description
- Claims
- Application Information
AI Technical Summary
Problems solved by technology
Method used
Image
Examples
Embodiment Construction
[0017] Attached below Figure 1 ~ Figure 4 The present invention will be further elaborated through specific examples, wherein the examples are descriptive and not restrictive, and cannot limit the scope of protection of the present invention.
[0018] figure 1 For the overall schematic diagram of the precision mold proposed by the present invention, as figure 1 As shown, the precision mold consists of the following parts from top to bottom: positioning ring 1, fixed template 2, fixed mold hot runner plate 3, fixed mold support plate 4, fixed mold insert adjustment plate 7, gate removal plate 8, The movable mold insert adjustment plate 9, the movable mold support plate 10, the ejector pin 11, the ejector plate 12, the movable mold back plate 13, the insert position adjustment servo cylinder 5 and the gate removal hydraulic cylinder 6. This embodiment focuses on the part of the precision mold that involves the realization of multiple injections of a single melt, omitting othe...
PUM
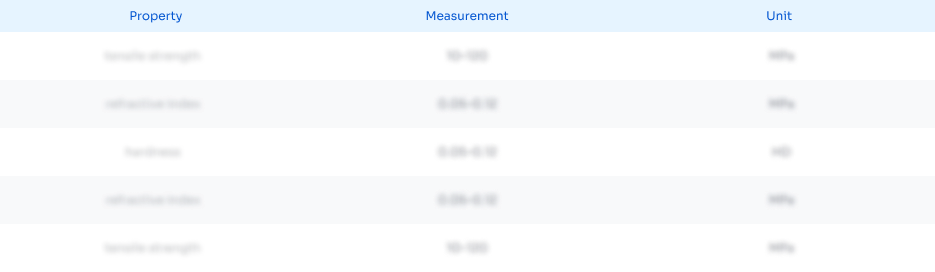
Abstract
Description
Claims
Application Information

- R&D
- Intellectual Property
- Life Sciences
- Materials
- Tech Scout
- Unparalleled Data Quality
- Higher Quality Content
- 60% Fewer Hallucinations
Browse by: Latest US Patents, China's latest patents, Technical Efficacy Thesaurus, Application Domain, Technology Topic, Popular Technical Reports.
© 2025 PatSnap. All rights reserved.Legal|Privacy policy|Modern Slavery Act Transparency Statement|Sitemap|About US| Contact US: help@patsnap.com