Fabric finishing agent, and preparation method thereof
A fabric finishing agent, technology in parts by weight, applied in fiber treatment, textiles and papermaking, wear-resistant fibers, etc., can solve harmful formaldehyde and other problems, achieve low toxicity, good economic benefits, safe and simple operation
- Summary
- Abstract
- Description
- Claims
- Application Information
AI Technical Summary
Problems solved by technology
Method used
Examples
Embodiment 1
[0035] The invention discloses a fabric finishing agent, which comprises the following components in parts by weight: 10 parts of butane tetraacid, 3 parts of ammonium citrate, 3 parts of sodium hexametaphosphate, 5 parts of diatomaceous earth, aspartic acid 3 parts, 3 parts of lignosulfonic acid, 3 parts of malic acid, 5 parts of plant essence, 5 parts of hydroxymethyl cellulose, 10 parts of amino silicone oil, 20 parts of deionized water.
[0036] The present invention also provides a kind of preparation method of fabric finishing agent, concrete steps are as follows:
[0037] (1) Add 10 parts of butane tetraacid, 3 parts of ammonium citrate, 10 parts of amino silicone oil, 20 parts of deionized water into the reaction kettle, stir at 900 rpm for 20 minutes;
[0038] (2) Add 3 parts of sodium hexametaphosphate, 5 parts of diatomaceous earth, 5 parts of hydroxymethylcellulose, 500 rpm, and stir for 30 minutes;
[0039] (3) Add 3 parts of aspartic acid and 3 parts of lignosul...
Embodiment 2
[0044] The invention discloses a fabric finishing agent, which comprises the following components in parts by weight: 15 parts of butane tetraacid, 4 parts of ammonium citrate, 4 parts of sodium hexametaphosphate, 6 parts of diatomaceous earth, aspartic acid 4 parts, lignosulfonic acid 4 parts, malic acid 4 parts, plant essence 6 parts, hydroxymethyl cellulose 8 parts, amino silicone oil 13 parts, deionized water 25 parts.
[0045] The present invention also provides a kind of preparation method of fabric finishing agent, concrete steps are as follows:
[0046] (1) Add 15 parts of butane tetraacid, 4 parts of ammonium citrate, 13 parts of amino silicone oil, 25 parts of deionized water into the reaction kettle, stir at 800 rpm for 25 minutes;
[0047] (2) Add 4 parts of sodium hexametaphosphate, 6 parts of diatomaceous earth, 8 parts of hydroxymethylcellulose, 800 rpm, and stir for 25 minutes;
[0048] (3) Add 4 parts of aspartic acid and 4 parts of lignosulfonic acid, stir a...
Embodiment 3
[0053] The invention discloses a fabric finishing agent, which comprises the following components in parts by weight: 20 parts of butane tetraacid, 5 parts of ammonium citrate, 5 parts of sodium hexametaphosphate, 7 parts of diatomaceous earth, aspartic acid 5 parts, lignosulfonic acid 5 parts, malic acid 5 parts, plant essence 7 parts, hydroxymethyl cellulose 10 parts, amino silicone oil 15 parts, deionized water 30 parts.
[0054] The present invention also provides a kind of preparation method of fabric finishing agent, concrete steps are as follows:
[0055] (1) Add 20 parts of butane tetraacid, 5 parts of ammonium citrate, 15 parts of amino silicone oil, 30 parts of deionized water into the reaction kettle, stir at 1000 rpm for 30 minutes;
[0056] (2) Add 5 parts of sodium hexametaphosphate, 7 parts of diatomaceous earth, 10 parts of hydroxymethylcellulose, 1000 rpm, and stir for 30 minutes;
[0057] (3) Add 5 parts of aspartic acid and 5 parts of lignosulfonic acid, st...
PUM
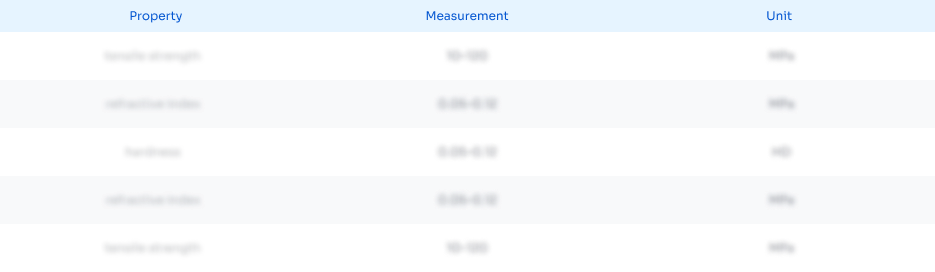
Abstract
Description
Claims
Application Information

- R&D
- Intellectual Property
- Life Sciences
- Materials
- Tech Scout
- Unparalleled Data Quality
- Higher Quality Content
- 60% Fewer Hallucinations
Browse by: Latest US Patents, China's latest patents, Technical Efficacy Thesaurus, Application Domain, Technology Topic, Popular Technical Reports.
© 2025 PatSnap. All rights reserved.Legal|Privacy policy|Modern Slavery Act Transparency Statement|Sitemap|About US| Contact US: help@patsnap.com