Ultrasonic motor driven by screw thread pair based on bending vibration mode and working method thereof
A technology of ultrasonic motor and thread pair, which is applied in the direction of piezoelectric effect/electrostrictive or magnetostrictive motor, generator/motor, electrical components, etc. Changes and other issues
- Summary
- Abstract
- Description
- Claims
- Application Information
AI Technical Summary
Problems solved by technology
Method used
Image
Examples
Embodiment Construction
[0018] The invention discloses a linear ultrasonic motor driven by a screw pair based on a bending vibration mode.
[0019] Embodiments of the present invention will be described in detail below, and the embodiments described herein with reference to the accompanying drawings are exemplary, and are only used to explain the present invention, rather than to limit the present invention.
[0020] A structural schematic diagram of a thread pair driven ultrasonic motor disclosed by the present invention is as follows: figure 1 As shown, it includes a stator 1 , a mover 2 , a base 3 and a preloading component 4 , wherein the mover includes: a mover main shaft 21 and a sleeve 22 . The base includes: a clamping seat end cover 31 and a clamping seat bottom plate 32 . The preload loading device includes: a preload bolt 41 and a preload spring 42 . The base 3 is assembled in the middle of the stator. The mover 2 is assembled inside the stator. The pre-pressure device 4 is assembled o...
PUM
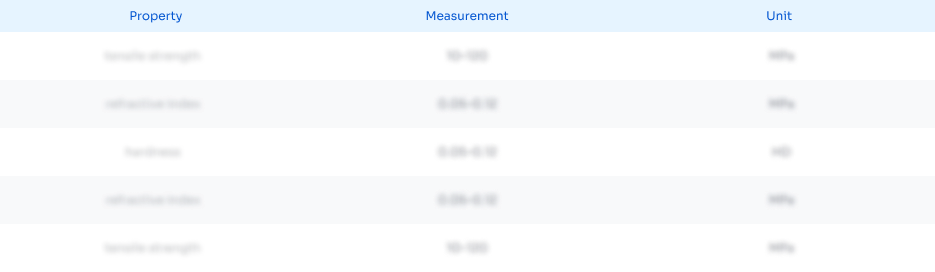
Abstract
Description
Claims
Application Information

- Generate Ideas
- Intellectual Property
- Life Sciences
- Materials
- Tech Scout
- Unparalleled Data Quality
- Higher Quality Content
- 60% Fewer Hallucinations
Browse by: Latest US Patents, China's latest patents, Technical Efficacy Thesaurus, Application Domain, Technology Topic, Popular Technical Reports.
© 2025 PatSnap. All rights reserved.Legal|Privacy policy|Modern Slavery Act Transparency Statement|Sitemap|About US| Contact US: help@patsnap.com