Numerical control machine tool kinematic chain design method considering nonlinear error and generalized modal
A non-linear error, CNC machine tool technology, applied in the field of CNC machine tools, can solve the problems of low motion efficiency, cannot be completely eliminated, and occupies a large working space.
- Summary
- Abstract
- Description
- Claims
- Application Information
AI Technical Summary
Problems solved by technology
Method used
Image
Examples
Embodiment Construction
[0073] The present invention will be described in further detail below in conjunction with accompanying drawings and examples.
[0074] Such as figure 1 Shown, the embodiment of the present invention and its implementation process are as follows:
[0075] Step (1): Construct a computational model for kinematic chain design to minimize the cumulative nonlinear error ∑ε non and minimize the reciprocal M of the generalized mode -1 To solve the target, initialize the kinematic chain configuration population algebra g, let g=1; model to minimize f 1 and minimize f 2 to solve the target.
[0076] Step (2): When g=1, randomly generate the g-generation kinematic chain configuration population, and initialize the individual number p of the kinematic chain configuration population, let p=1; when g>1, for the g-1th generation The population is selected, crossed, and mutated to generate the g-generation kinematic chain configuration population;
[0077] Each population is composed o...
PUM
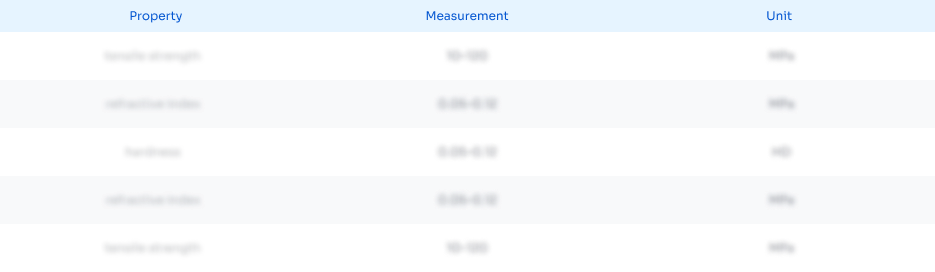
Abstract
Description
Claims
Application Information

- R&D
- Intellectual Property
- Life Sciences
- Materials
- Tech Scout
- Unparalleled Data Quality
- Higher Quality Content
- 60% Fewer Hallucinations
Browse by: Latest US Patents, China's latest patents, Technical Efficacy Thesaurus, Application Domain, Technology Topic, Popular Technical Reports.
© 2025 PatSnap. All rights reserved.Legal|Privacy policy|Modern Slavery Act Transparency Statement|Sitemap|About US| Contact US: help@patsnap.com