Novel LED heat dissipating lamp shell for daily lighting and production method thereof
A production method and heat dissipation lamp technology, applied in the cooling/heating device of lighting devices, lighting and heating equipment, components of lighting devices, etc., can solve problems such as leakage, long production cycle, and difficulty in meeting safety standards, and achieve Increase the heat dissipation surface area, improve the aging resistance performance, and optimize the heat dissipation effect of the whole lamp
- Summary
- Abstract
- Description
- Claims
- Application Information
AI Technical Summary
Problems solved by technology
Method used
Image
Examples
Embodiment 1
[0036] Add a total of 400g of acetylene carbon black, conductive furnace black, single-walled carbon nanotubes, 500g of water, 10g of sodium hyaluronate, acid red and sodium dodecyl dinaphthyl ether sulfonate into the container, and use a high-speed shear emulsifier Shear and stir at 2500rpm for 2 hours to obtain a viscous mixture, remove part of the solvent of the above-mentioned viscous mixture by suction filtration and drying, and obtain a viscous mixture with a viscosity of 150cP, and transfer the obtained viscous mixture to the outer layer by brushing On the inner surface of the plastic, use 5 MPa to centrifugally roll the outer plastic inner surface until an inner surface film with a thickness of 0.06mm is formed, heat the LED lamp housing in a 50°C oven for more than 30 minutes, and then repeat the above transfer, rolling and heating Step 9 times to obtain an inner heat conduction film with a final thickness of 0.6 mm, and roll the inner heat conduction film in a heating...
Embodiment 2
[0038] A total of 600g of graphene, multi-walled carbon nanotubes, acetylene carbon black, 800g of water, 150g of starch, allura red, quinoline yellow and sodium naphthalene disulfonate were added to the container, mixed and stirred for 5 hours to obtain a viscous mixed solution, and heated Part of the solvent of the above-mentioned viscous mixed solution is removed by drying to obtain a viscous mixed solution with a viscosity of 2500cP. The viscous mixed solution obtained is transferred to the inner surface of the outer plastic by spraying, and the inner surface of the outer plastic is rolled with a pressure of 30MPa until it is formed. For an inner surface film with a thickness of 0.01mm, heat the LED lamp housing in an oven at 40°C for more than 25 minutes, and then repeat the above steps of transfer, rolling and heating 19 times to obtain an inner layer heat conduction film with a final thickness of 0.2mm. The inner heat conduction film is subjected to centrifugal rolling u...
Embodiment 3
[0040] Add a total of 80g of expanded graphite and natural graphite, 200g of water, 20g of starch, quinoline yellow, carmine and sodium cetyl diphenyl ether disulfonate into the container, mix for 4 hours with a ball mill to obtain a viscous mixture, and heat Part of the solvent of the above-mentioned viscous mixed solution was removed by drying to obtain a viscous mixed solution with a viscosity of 1000cP. The obtained viscous mixed solution was transferred to the inner surface of the outer plastic by scraping method, and the inner surface of the outer plastic was pressed with a pressure of 60MPa until Form an inner surface film with a thickness of 0.1mm, heat the LED lamp housing in an oven at 20°C for more than 5 minutes, then repeat the above steps of transferring, rolling and heating 4 times to obtain an inner layer heat conducting film with a final thickness of 0.5mm, The inner heat conduction film was subjected to centrifugal rolling under a pressure of 80 MPa in a heati...
PUM
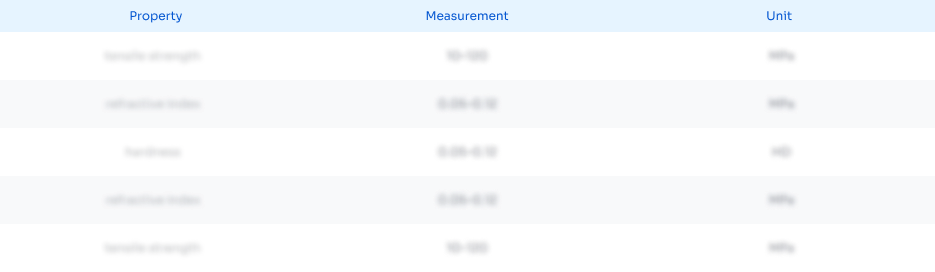
Abstract
Description
Claims
Application Information

- R&D
- Intellectual Property
- Life Sciences
- Materials
- Tech Scout
- Unparalleled Data Quality
- Higher Quality Content
- 60% Fewer Hallucinations
Browse by: Latest US Patents, China's latest patents, Technical Efficacy Thesaurus, Application Domain, Technology Topic, Popular Technical Reports.
© 2025 PatSnap. All rights reserved.Legal|Privacy policy|Modern Slavery Act Transparency Statement|Sitemap|About US| Contact US: help@patsnap.com