Positioning device and method for pipeline detection
A technology of pipeline detection and positioning device, applied in pipeline system, navigation through velocity/acceleration measurement, mechanical equipment, etc., can solve the problems of inability to apply long-distance pipeline detection, inability to guarantee measurement accuracy, and impact on measurement accuracy, and achieve a reduction in Cost and energy consumption, ensure stability, improve the effect of measurement accuracy
- Summary
- Abstract
- Description
- Claims
- Application Information
AI Technical Summary
Problems solved by technology
Method used
Image
Examples
specific Embodiment approach 1
[0056] Specific Embodiment 1: Combining figure 1 and figure 2 Describe this embodiment, a positioning device for pipeline detection in this embodiment, the specific structure is as follows figure 1 As shown, it includes: power supply module 1, two support wheels 2, first plastic sealing ring 3, inertial measurement module 4, data processing unit 5, second plastic sealing ring 6, data storage unit 7, odometer 8, magnetic flux Leak sensor 9 , communication cable 10 and magnetic tracking module 11 .
[0057] The power supply module 1, inertial measurement module 4, data processing module 5 and data storage module 7 are arranged in sequence from front to back, and are fixed as a whole by the first plastic sealing ring 3 and the second plastic sealing ring 6 outside.
[0058] The power supply module 1 provides electric energy for the positioning device for pipeline detection to ensure its normal operation.
[0059] The structure of the inertial measurement module 4 is as figu...
specific Embodiment approach 2
[0067] Specific Embodiment 2: Combining image 3 Describe this embodiment, the flow chart of the positioning method of this embodiment is as follows image 3 As shown, the specific steps include:
[0068] Step a, turn on the power supply module 1, and initialize the positioning device for pipeline detection;
[0069] Step b, make the positioning device for pipeline detection go through the pipeline once, and use the x-direction accelerometer, y-direction accelerometer, fiber optic gyroscope and odometer 8 to measure the roll angle, pitch angle, and orientation of the pipeline detection positioning device respectively Angle and axial velocity, using the magnetic flux leakage sensor 9 to detect pipeline defect information, simple processing of each measured value data through the data processing unit 5, and storing the processed data through the data storage unit 7;
[0070] Step c, combining the output data of the x-direction accelerometer, the y-direction accelerometer, the ...
PUM
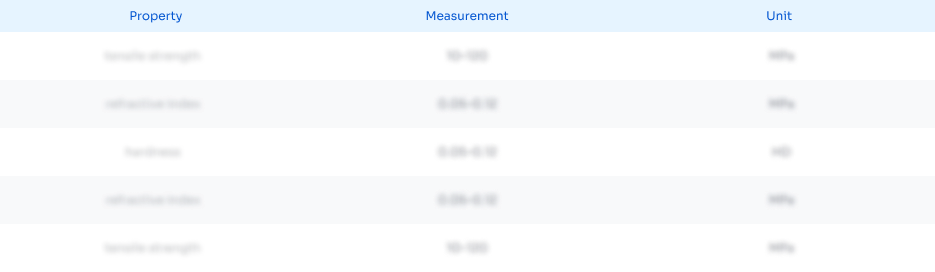
Abstract
Description
Claims
Application Information

- R&D Engineer
- R&D Manager
- IP Professional
- Industry Leading Data Capabilities
- Powerful AI technology
- Patent DNA Extraction
Browse by: Latest US Patents, China's latest patents, Technical Efficacy Thesaurus, Application Domain, Technology Topic, Popular Technical Reports.
© 2024 PatSnap. All rights reserved.Legal|Privacy policy|Modern Slavery Act Transparency Statement|Sitemap|About US| Contact US: help@patsnap.com