Space fluid velocity and pressure synchronous measurement system based on pressure-sensitive particle light intensity measurement
A fluid velocity and synchronous measurement technology, applied in the direction of measuring devices, instruments, etc., can solve the problems of complex flow field and increased pressure distribution of pneumatic components
- Summary
- Abstract
- Description
- Claims
- Application Information
AI Technical Summary
Problems solved by technology
Method used
Image
Examples
Embodiment 1
[0042] Such as figure 1 As shown, the space fluid velocity pressure synchronous measurement system based on pressure-sensitive particle light intensity measurement includes a signal transmitter 8, a pulsed laser generator (that is, a 400nm laser generator) 6 electrically connected to the signal transmitter 8, a particle source 3, A particle generator 2 used in conjunction with a particle source 3, and an image processing unit, the image processing unit includes a filter 4, a high-speed CCD camera 5, a computer 1 connected to the high-speed CCD camera 5;
[0043] Among them, the pressure-sensitive particles include hollow SiO 2 Particles, Hollow SiO 2 Pressure-sensitive luminescent molecules are adsorbed on the surface of the particles, and distributed into the space to be measured through the particle generator 2 .
[0044] In this embodiment, the size of the pressure-sensitive particle is 10 μm, and the attached pressure-sensitive luminescent molecule is PtTFPP. The prepar...
Embodiment 2
[0056] Such as figure 2 As shown, the pressure calibration system of the present invention includes a signal transmitter 8, a 400nm laser generator 6 electrically connected to the signal transmitter 8, a pressure-sensitive particle sample 9, a pressure control box 10, and an image processing unit. This image processing unit comprises filter mirror 4, high-speed CCD camera 5, the computer 1 that is connected with high-speed CCD camera 5
[0057] Firstly, the pressure-sensitive luminescent molecules were dissolved in dichloromethane solvent, and then hollow SiO 2 particles (control concentration is 0.15g / mL), and then the pressure-sensitive dye photons are adsorbed on the hollow SiO by ultrasonic vibration. 2 Particles, filtered and evaporated to dryness.
[0058] Wherein, dichloromethane is used as solvent, and the concentration of PtTFPP is 2mg / ml and Ru(dpp) respectively. 3 A solution with a concentration of 1 mg / ml. Two sizes of particles (wherein the larger particle ha...
Embodiment 3
[0062] Such as image 3 The present invention is shown in the structure diagram of the adjustable space flow field measurement system, the measurement system includes a signal transmitter 8, a pulsed laser generator 6 electrically connected to the signal transmitter 8, a particle source 3, used in conjunction with the particle source 3 The particle generator 2, and the image processing unit, the image processing unit includes a filter 4, a high-speed CCD camera 5, a computer 1 connected to the high-speed CCD camera 5, and a piston 12 and a piston sleeve 11 for controlling pressure.
[0063] In this embodiment, the size of the pressure-sensitive particle is 2 μm, and the attached pressure-sensitive luminescent molecule is PtTFPP.
[0064] In this embodiment, the pressure in the flow field of the pressure stabilizing space is adjusted by controlling the piston.
[0065] In the working state, the pressure-sensitive particles in the particle source 3 are evenly implanted into the...
PUM
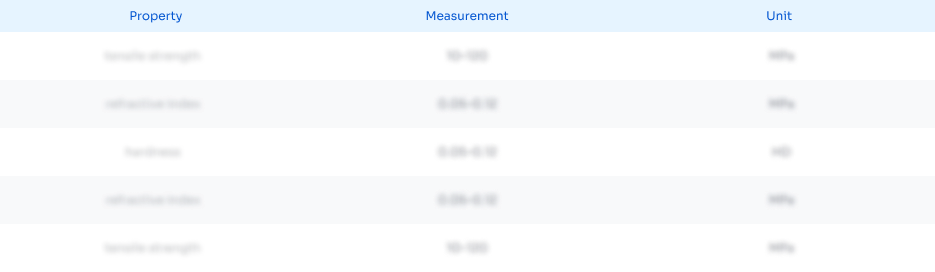
Abstract
Description
Claims
Application Information

- Generate Ideas
- Intellectual Property
- Life Sciences
- Materials
- Tech Scout
- Unparalleled Data Quality
- Higher Quality Content
- 60% Fewer Hallucinations
Browse by: Latest US Patents, China's latest patents, Technical Efficacy Thesaurus, Application Domain, Technology Topic, Popular Technical Reports.
© 2025 PatSnap. All rights reserved.Legal|Privacy policy|Modern Slavery Act Transparency Statement|Sitemap|About US| Contact US: help@patsnap.com