Local matt and light heat transfer film preparation process
A thermal transfer printing film and technology of preparation process, which is applied in the printing process, printing of special varieties of printed matter, printing, etc., can solve the problem of large consumption, and achieve the effect of clear lines and bright colors
- Summary
- Abstract
- Description
- Claims
- Application Information
AI Technical Summary
Problems solved by technology
Method used
Examples
Embodiment Construction
[0020] The preferred embodiments of the present invention are described in detail below, so that the advantages and features of the present invention can be more easily understood by those skilled in the art, so as to define the protection scope of the present invention more clearly.
[0021] The present invention is a preparation process of a partially matte and glossy thermal transfer printing film, comprising the following steps:
[0022] 1) Engraving matte pattern plate line: engrave 175 mesh matte pattern plate line on the anilox roller;
[0023] 2) Apply matte coating: use weight percentages of acrylic copolymer 30%-35%, silicon 3%-5%, ethyl acetate 45%-55%, butyl acetate 5%, matte coating curing 15%-18% additives to make a matte coating, and pass through a 7-meter-long horizontal oven. There are four sets of horizontal ovens, the temperature is 70°C-75°C, and the machine speed is 100-120 m / min;
[0024] 3) Curing in a constant temperature oven: After coating the matte ...
PUM
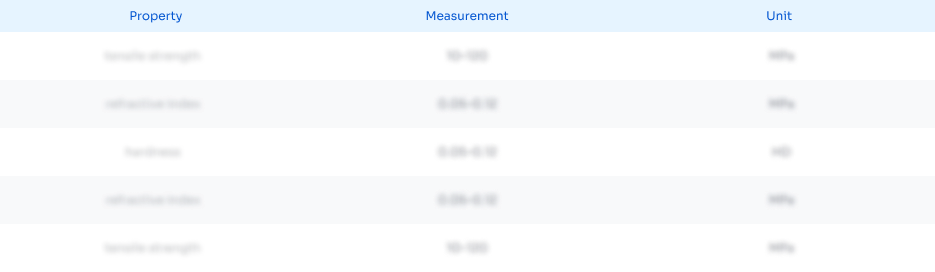
Abstract
Description
Claims
Application Information

- Generate Ideas
- Intellectual Property
- Life Sciences
- Materials
- Tech Scout
- Unparalleled Data Quality
- Higher Quality Content
- 60% Fewer Hallucinations
Browse by: Latest US Patents, China's latest patents, Technical Efficacy Thesaurus, Application Domain, Technology Topic, Popular Technical Reports.
© 2025 PatSnap. All rights reserved.Legal|Privacy policy|Modern Slavery Act Transparency Statement|Sitemap|About US| Contact US: help@patsnap.com