High-strength and high-toughness epoxy resin
An epoxy resin, high toughness technology, applied in the field of polymer materials, can solve the problems of high cost and limited effect of improving the mechanical properties of epoxy resin, and achieve the effect of improving strength and toughness
- Summary
- Abstract
- Description
- Claims
- Application Information
AI Technical Summary
Problems solved by technology
Method used
Image
Examples
Embodiment 1
[0028] 100g of four-functional epoxy epoxy resin, 19g of epoxy octadecane, 95g of hexahydrophthalic anhydride, and 0.48g of quaternary ammonium salt are mixed in a beaker, placed in a constant temperature oil bath and stirred at a medium speed for 10min, vacuumed to remove air bubbles, that is, press 90°C / After 3h+130℃ / 3h pouring and curing, the cured epoxy resin can be obtained, and the mechanical properties are shown in Table 1.
Embodiment 2
[0030] Four functional epoxy epoxy resin 100g, 3,4-epoxycyclohexylmethyl-3,4-epoxycyclohexyl carboxylate 10g, methyl nadic anhydride 123g, and DMP-30 accelerator 2.33g mixed Place the beaker in a constant temperature oil bath and stir at medium speed for 10 minutes, vacuumize to remove air bubbles, and pour and cure at 90°C / 3h+130°C / 3h to obtain cured epoxy resin. The mechanical properties are shown in Table 1.
Embodiment 3
[0032] 100g of bisphenol F epoxy resin, 5g of glycidyl stearate, 96g of nadic acid anhydride, and 1.45g of N-diglycidyl aniline accelerator were mixed in a beaker, placed in a constant temperature oil bath and stirred at medium speed for 10min, vacuumed to remove air bubbles, That is, pour and cure at 90°C / 3h+130°C / 3h to obtain a cured epoxy resin. The mechanical properties are listed in Table 1.
PUM
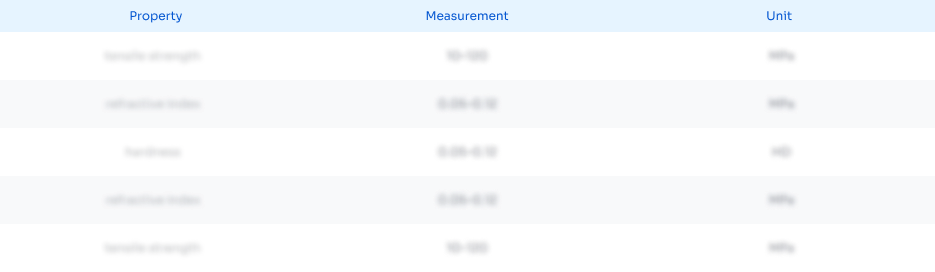
Abstract
Description
Claims
Application Information

- R&D Engineer
- R&D Manager
- IP Professional
- Industry Leading Data Capabilities
- Powerful AI technology
- Patent DNA Extraction
Browse by: Latest US Patents, China's latest patents, Technical Efficacy Thesaurus, Application Domain, Technology Topic, Popular Technical Reports.
© 2024 PatSnap. All rights reserved.Legal|Privacy policy|Modern Slavery Act Transparency Statement|Sitemap|About US| Contact US: help@patsnap.com