Elastic speed reducer
A reducer and elastic technology, which is applied in the field of elastic reducers, can solve the problems of large reducers, insufficient rigidity, and large rotational inertia, so as to ensure the center output, eliminate radial assembly errors and parts processing errors, and improve precision. Effect
- Summary
- Abstract
- Description
- Claims
- Application Information
AI Technical Summary
Problems solved by technology
Method used
Image
Examples
Embodiment 1
[0046] Such as figure 1 , 2 , 3, this embodiment discloses an elastic reducer, including a power input assembly, the power input assembly includes an input shaft 1, an elastic assembly arranged on the input shaft 1, and the elastic assembly is an extrusion-type deformation The extrusion-type deformation ring includes an annular ring body 2, and an elastic structural member is provided on the outer ring wall of the annular ring body.
[0047] In this embodiment, the above-mentioned elastic structure includes two shrapnel groups symmetrical to each other, and each shrapnel group includes a number of first shrapnel groups and second shrapnel groups distributed on the outer ring wall of the annular ring, and the outer ring of the ring ring The wall is provided with an elastic limit boss 23, the first shrapnel group and the outer ring wall of the annular ring form an angle that is biased toward the elastic limit boss, and the second shrapnel group forms an opposite angle to the ou...
Embodiment 2
[0075] refer to figure 1 , 2 , this embodiment is similar to Embodiment 1, disclosing an elastic reducer, including a power input assembly, the power input assembly includes an input shaft 1, an elastic assembly arranged on the input shaft 1, and the elastic assembly is an extrusion One of the differences from Embodiment 1 is that the inner ring wall of the annular ring body is provided with an elastic structural member.
[0076] In this embodiment, the above-mentioned elastic structure includes two shrapnel groups that are symmetrical to each other, and each shrapnel group includes a number of first shrapnel groupings and second shrapnel groupings distributed on the inner wall of the annular ring. There is an elastic limit boss, the first shrapnel group and the ring wall inside the annular ring form an angle that is biased towards the elastic limit boss, and the second shrapnel group and the inner ring wall of the annular ring form a reverse elastic limit boss angle. Each ...
PUM
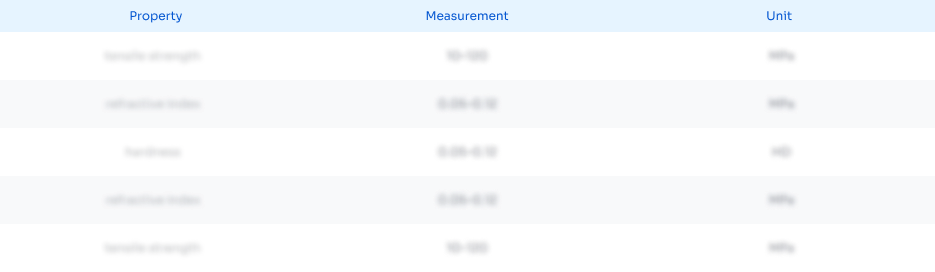
Abstract
Description
Claims
Application Information

- R&D
- Intellectual Property
- Life Sciences
- Materials
- Tech Scout
- Unparalleled Data Quality
- Higher Quality Content
- 60% Fewer Hallucinations
Browse by: Latest US Patents, China's latest patents, Technical Efficacy Thesaurus, Application Domain, Technology Topic, Popular Technical Reports.
© 2025 PatSnap. All rights reserved.Legal|Privacy policy|Modern Slavery Act Transparency Statement|Sitemap|About US| Contact US: help@patsnap.com