Cotton fiber continuously-dyeing method
A dyeing method and cotton fiber technology, which is applied in the field of fiber dyeing, can solve the problems of low production efficiency, low strength of dyed cotton, and poor spinnability, etc., and achieve the effects of small decrease in specific strength at break, improvement of spinnability, and reduction of strength loss
- Summary
- Abstract
- Description
- Claims
- Application Information
AI Technical Summary
Problems solved by technology
Method used
Image
Examples
Embodiment 1
[0038] (1) Preparation of combed sliver
[0039] The untreated raw cotton loose fibers are opened 4 times by the blowing and carding machine, and then combed to prepare combed cotton slivers;
[0040] (2) Dyeing
[0041] Inject the prepared dye solution into the liquid-sealed gap of the rollers of the horizontal padder, then dip the combed cotton sliver prepared in step (1) into the dye solution and place it at 30°C for 12 hours. The combed cotton sliver has a liquid rate of 85%. %.
[0042] Wherein said dye liquor is made up of 30g / L monovinyl sulfone active red, 3g / L monovinyl sulfone active orange, 10g / L monovinyl sulfone active blue, 23g / L Serapol LR-01, 5g / L homogeneous The dye is mixed evenly;
[0043] (3) Washing
[0044] Put the cotton slivers that have been piled up for 12 hours in step (2) in an industrial elution machine, and wash them with water according to the following procedure: 5 minutes in cold water at 25°C, 3 minutes in hot water at 90°C, and 5 minutes ...
Embodiment 2
[0047] (1) Preparation of combed sliver
[0048] Combed cotton slivers are prepared by combing the untreated raw cotton loose fibers through the blowing and carding machine for 5 times;
[0049] (2) Dyeing
[0050] Inject the prepared dye solution into the liquid-sealed gap of the rollers of the horizontal padder, then dip the combed cotton sliver prepared in step (1) into the dye solution and stack it at 30°C for 10 hours, and the combed cotton sliver liquid rate is 90%. %;
[0051] Among them, the dye solution is 40g / L monovinyl sulfone reactive red, 11g / L monovinyl sulfone reactive orange, 3g / L monovinyl sulfone reactive blue, 23g / L Serapol LR-01, 5g / L leveling agent mixed Uniform;
[0052] (3) Washing
[0053] Put the cotton slivers that have been piled up for 10 hours in step (2) in an industrial elution machine, and wash them with water according to the following procedure: 5 minutes in cold water at 25°C, 3 minutes in hot water at 90°C, and 5 minutes in cold water a...
Embodiment 3
[0056] (1) Preparation of combed sliver
[0057]Combed cotton slivers were prepared by combing untreated raw cotton loose fibers through a blowing-carding machine for 4 times and then combing.
[0058] (2) Dyeing
[0059] Inject the prepared dye solution into the liquid-sealed gap of the rollers of the horizontal padder, then dip the combed cotton sliver prepared in step (1) into the dye solution and place it at 30°C for 18 hours, and the combed cotton sliver has a liquid rate of 95%. %;
[0060] The monovinyl sulfone reactive red of the dye solution 60g / L, the monovinyl sulfone reactive orange of 16g / L, the monovinyl sulfone reactive blue of 5g / L, 23g / L color fast LR-01, 5g / L level dyeing The agent is mixed evenly.
[0061] (3) Washing
[0062] Put the cotton slivers that have been piled up for 18 hours in step (2) in an industrial elution machine, and wash them with water according to the following procedure: 5 minutes in cold water at 25°C, 3 minutes in hot water at 90°...
PUM
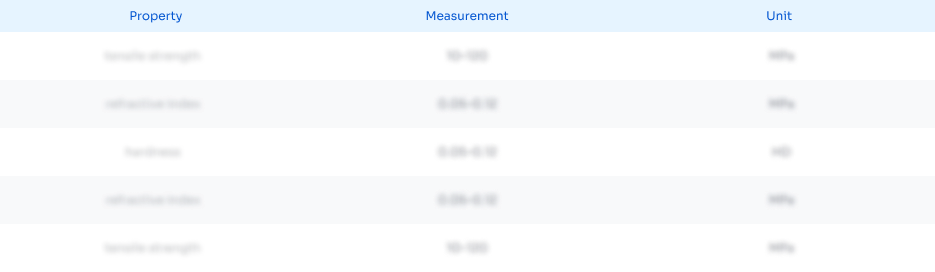
Abstract
Description
Claims
Application Information

- R&D
- Intellectual Property
- Life Sciences
- Materials
- Tech Scout
- Unparalleled Data Quality
- Higher Quality Content
- 60% Fewer Hallucinations
Browse by: Latest US Patents, China's latest patents, Technical Efficacy Thesaurus, Application Domain, Technology Topic, Popular Technical Reports.
© 2025 PatSnap. All rights reserved.Legal|Privacy policy|Modern Slavery Act Transparency Statement|Sitemap|About US| Contact US: help@patsnap.com