Preparation method for regenerating base oil from waste lubrication oil
A technology for regenerating base oil and waste lubricating oil, applied in lubricating compositions and other directions, can solve the problems of poor product quality, hazardous waste pollution in the clay environment, and unqualified products, so as to solve the problem of secondary pollution and reduce hazardous waste pollution. , The effect of large operational flexibility
- Summary
- Abstract
- Description
- Claims
- Application Information
AI Technical Summary
Problems solved by technology
Method used
Examples
Embodiment 1
[0028] 1) Preprocessing
[0029] Pump the waste lubricating oil into the settling tank with stirring, stir for 10~60min, heat up at the same time, keep the waste lubricating oil at 60~80℃ for 2~12h, and the acid value exceeds 0.05mg KOH / g waste lubricating oil Add 0.5~10% caustic soda to neutralize to 0.05mg KOH / g waste lubricating oil; continue to heat up to 100~120°C, turn on the vacuum pump to draw negative pressure, and keep the pressure at 0.09Mpa for 2 hours, so that the water content reaches within 0.5%. into raw material oil, and then pumped into the raw material tank for temporary storage. This step is used to dehydrate the waste lubricating oil.
[0030] In this embodiment, the stirring time is 30 minutes, the standing settling temperature is 70° C., and the settling time is 10 hours; the vacuum dehydration temperature is 110° C.
[0031] 2) Flash degassing
[0032] The pretreated raw oil is preheated by a heat exchanger to above 140°C and enters into a flash towe...
Embodiment 2
[0046] 1) Preprocessing
[0047] Pump the waste lubricating oil into the settling tank with stirring, stir for 10~60min, heat up at the same time, keep the waste lubricating oil at 60~80℃ for 2~12h, and the acid value exceeds 0.05mg KOH / g waste lubricating oil Add 0.5~10% caustic soda to neutralize to 0.05mg KOH / g waste lubricating oil; continue to heat up to 100~120°C, turn on the vacuum pump to draw negative pressure, and keep the pressure at 0.09Mpa for 2 hours, so that the water content reaches within 0.5%. into raw material oil, and then pumped into the raw material tank for temporary storage. This step is used to dehydrate the waste lubricating oil.
[0048]In this embodiment, the stirring time is 60 minutes, the standing settling temperature is 80°C, and the settling time is 12h; the vacuum dehydration temperature is 120°C.
[0049] 2) Flash degassing
[0050] The pretreated raw oil is preheated by a heat exchanger to above 140°C and enters into a flash tower, where ...
Embodiment 3
[0064] 1) Preprocessing
[0065] Pump the waste lubricating oil into the settling tank with stirring, stir for 10~60min, heat up at the same time, keep the waste lubricating oil at 60~80℃ for 2~12h, and the acid value exceeds 0.05mg KOH / g waste lubricating oil Add 0.5~10% caustic soda to neutralize to 0.05mg KOH / g waste lubricating oil; continue to heat up to 100~120°C, turn on the vacuum pump to draw negative pressure, and keep the pressure at 0.09Mpa for 2 hours, so that the water content reaches within 0.5%. into raw material oil, and then pumped into the raw material tank for temporary storage. This step is used to dehydrate the waste lubricating oil.
[0066] In this embodiment, the stirring time is 10 min, the standing settling temperature is 60°C, and the settling time is 2h; the vacuum dehydration temperature is 100°C.
[0067] 2) Flash degassing
[0068] The pretreated raw oil is preheated by a heat exchanger to above 140°C and enters into a flash tower, where the ...
PUM
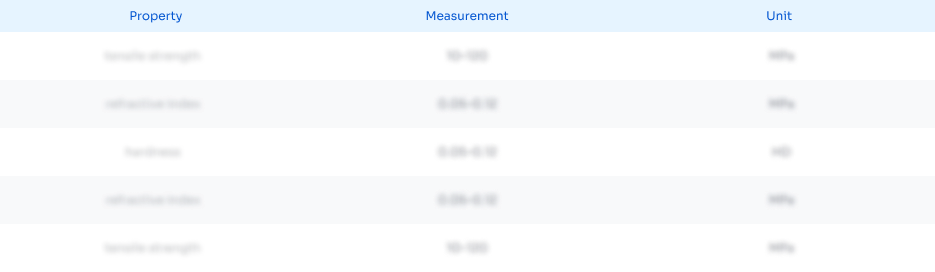
Abstract
Description
Claims
Application Information

- R&D Engineer
- R&D Manager
- IP Professional
- Industry Leading Data Capabilities
- Powerful AI technology
- Patent DNA Extraction
Browse by: Latest US Patents, China's latest patents, Technical Efficacy Thesaurus, Application Domain, Technology Topic, Popular Technical Reports.
© 2024 PatSnap. All rights reserved.Legal|Privacy policy|Modern Slavery Act Transparency Statement|Sitemap|About US| Contact US: help@patsnap.com