Fault-tolerant dual-vector prediction control method and apparatus for six-phase permanent magnet motor
A permanent magnet motor, fault-tolerant control technology, applied in the field of electromechanical, can solve the problems of limited number of action vectors, increased calculation amount, large current harmonic content, etc., to achieve the effect of increasing the output range and reducing the current harmonic content
- Summary
- Abstract
- Description
- Claims
- Application Information
AI Technical Summary
Problems solved by technology
Method used
Image
Examples
Embodiment Construction
[0062] In order to make the object, technical solution and advantages of the present invention clearer, the present invention will be further described in detail below in conjunction with the accompanying drawings and embodiments. It should be understood that the specific embodiments described here are only used to explain the present invention, not to limit the present invention. In addition, the technical features involved in the various embodiments of the present invention described below can be combined with each other as long as they do not constitute a conflict with each other.
[0063] In order to overcome the shortcomings of the traditional multi-phase permanent magnet motor fault-tolerant predictive control, the present invention provides a new type of fault-tolerant double-vector predictive control method, which establishes the motor mathematical model under the open-circuit fault of the partial winding of the motor in the phase winding coordinate system. The voltage...
PUM
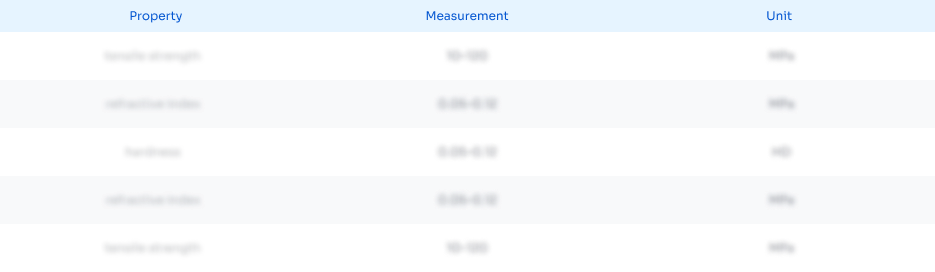
Abstract
Description
Claims
Application Information

- R&D
- Intellectual Property
- Life Sciences
- Materials
- Tech Scout
- Unparalleled Data Quality
- Higher Quality Content
- 60% Fewer Hallucinations
Browse by: Latest US Patents, China's latest patents, Technical Efficacy Thesaurus, Application Domain, Technology Topic, Popular Technical Reports.
© 2025 PatSnap. All rights reserved.Legal|Privacy policy|Modern Slavery Act Transparency Statement|Sitemap|About US| Contact US: help@patsnap.com