Welding strip structure applied to lamination assemblies
A technology of laminated components and ribbons, which is applied in electrical components, semiconductor devices, photovoltaic power generation, etc., can solve problems such as hidden cracks, inability to meet the production capacity requirements of fast stringing welding, and high requirements for automatic stringing welding
- Summary
- Abstract
- Description
- Claims
- Application Information
AI Technical Summary
Problems solved by technology
Method used
Image
Examples
Embodiment Construction
[0030] The invention or the invention will be described in detail below with reference to the accompanying drawings and specific embodiments. It should be noted that the data in the embodiments (such as the width and number of fine grids, etc.) can be adjusted according to actual conditions.
[0031] In the Smartwire module, the round ribbon 7 is circular and has a size of about 300 μm. It is bonded to the cell through a transparent polymer film as a carrier, such as Figure 4 As shown; during lamination, the welding strip is vertically welded to the fine grid line 6 by pressure and temperature to form good electrical properties. When the Smartwire technology is used in the lamination technology, the direction of the thin grid line 6 needs to be adjusted so that it is perpendicular to the direction of the solder strip. When the traditional Smartwire ribbon is used for lamination, its contact with the battery sheet is point contact. In the load and thermal stress related tests,...
PUM
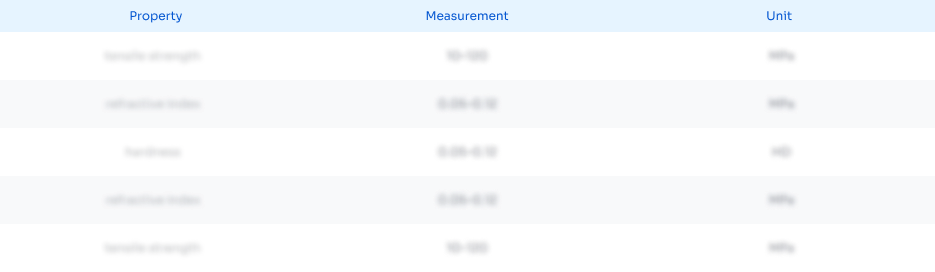
Abstract
Description
Claims
Application Information

- R&D Engineer
- R&D Manager
- IP Professional
- Industry Leading Data Capabilities
- Powerful AI technology
- Patent DNA Extraction
Browse by: Latest US Patents, China's latest patents, Technical Efficacy Thesaurus, Application Domain, Technology Topic, Popular Technical Reports.
© 2024 PatSnap. All rights reserved.Legal|Privacy policy|Modern Slavery Act Transparency Statement|Sitemap|About US| Contact US: help@patsnap.com