Cages for crankshaft bearing assemblies
A bearing assembly and cage technology, applied in the field of crankshaft bearing assemblies, connecting rods and/or main shaft bearing assemblies of crankshafts, to avoid lubricant accumulation, reduce motion, and reduce friction
- Summary
- Abstract
- Description
- Claims
- Application Information
AI Technical Summary
Problems solved by technology
Method used
Image
Examples
Embodiment Construction
[0029] figure 1A perspective section through a rolling element bearing assembly 1 is shown, which in the shown case is designed as a crankshaft bearing assembly. as from figure 1 As can be seen in the figure, a rolling element bearing 6 is arranged in a connecting rod eye 4 of the connecting rod 2 or in the housing 4 for the crankshaft. The rolling element bearing 6 ensures the rolling of the connecting rod 2 or housing 4 along the crankshaft 8 . here, as from figure 1 As can be seen in the rolling element bearing assembly 6, the outer raceway 12 on which the rolling elements 10 roll is formed above the connecting rod bore or housing 4, while the inner raceway 14 is shown on the crankpin 16 of the crankshaft 8 above. The crankpin 16 is in turn arranged between two crankshaft cheeks 18 , 20 which extend axially beyond the outer race surface 12 of the connecting rod bore 4 .
[0030] The installation space available for the rolling element bearing 6 is limited by the height...
PUM
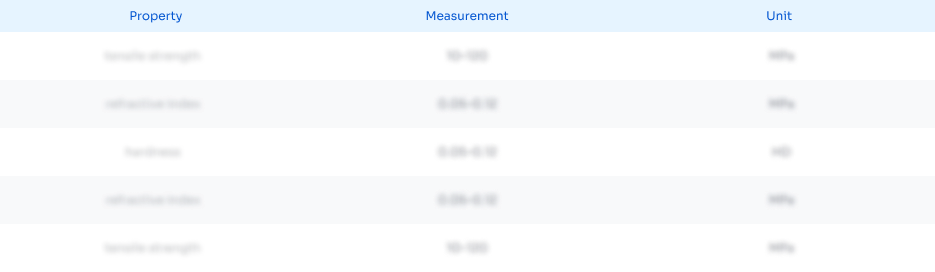
Abstract
Description
Claims
Application Information

- R&D Engineer
- R&D Manager
- IP Professional
- Industry Leading Data Capabilities
- Powerful AI technology
- Patent DNA Extraction
Browse by: Latest US Patents, China's latest patents, Technical Efficacy Thesaurus, Application Domain, Technology Topic, Popular Technical Reports.
© 2024 PatSnap. All rights reserved.Legal|Privacy policy|Modern Slavery Act Transparency Statement|Sitemap|About US| Contact US: help@patsnap.com