A process for preparing high-purity microcrystalline graphite in large quantities with low energy consumption and high-purity microcrystalline graphite
A microcrystalline graphite, large-scale technology, applied in carbon compounds, inorganic chemistry, chemical instruments and methods, etc., can solve the problems of high energy consumption and cost, low purity of microcrystalline graphite, etc., to reduce energy consumption and cost, reduce Energy consumption and the effect of increasing the specific surface area
- Summary
- Abstract
- Description
- Claims
- Application Information
AI Technical Summary
Problems solved by technology
Method used
Image
Examples
Embodiment 1
[0033] This embodiment provides a process for preparing high-purity microcrystalline graphite in large quantities with low energy consumption, comprising the following steps:
[0034] S1. Raw ore treatment: crush the microcrystalline graphite raw ore, and then carry out deep grinding on the microcrystalline graphite raw ore, and obtain the material with a fineness of -0.074mm through grinding, and the content of the material with a grinding fineness of -0.074mm accounts for 90% % of the raw ore samples are subjected to flotation, using a roughing process, four selections, and a sweeping process, followed by drying and magnetic separation to obtain microcrystalline graphite with a fixed carbon content of 90%;
[0035] In the raw ore treatment of this embodiment, the raw ore of microcrystalline graphite is Lutang graphite, wherein the moisture is 2.4%, the volatile matter is 2.99%, the ash content is 18.37%, and the carbon content is 78.64%;
[0036] S2. Purification by acid lea...
Embodiment 2
[0044] This embodiment provides a process for preparing high-purity microcrystalline graphite in large quantities with low energy consumption, comprising the following steps:
[0045] S1. Raw ore treatment: crush the microcrystalline graphite raw ore, and then carry out deep grinding on the microcrystalline graphite raw ore, and obtain the material with a fineness of -0.074mm through grinding, and the content of the material with a grinding fineness of -0.074mm accounts for 90% % of the raw ore samples are subjected to flotation, using a roughing process, four selections, and a sweeping process, followed by drying and magnetic separation to obtain microcrystalline graphite with a fixed carbon content of 90%;
[0046] In the raw ore treatment of this embodiment, the raw ore of microcrystalline graphite is Lutang graphite, wherein the moisture is 2.4%, the volatile matter is 2.99%, the ash content is 18.37%, and the carbon content is 78.64%;
[0047] S2. Purification by acid lea...
Embodiment 3
[0055] This embodiment provides a process for preparing high-purity microcrystalline graphite in large quantities with low energy consumption, comprising the following steps:
[0056] S1. Raw ore treatment: crush the microcrystalline graphite raw ore, and then carry out deep grinding on the microcrystalline graphite raw ore, and obtain the material with a fineness of -0.074mm through grinding, and the content of the material with a grinding fineness of -0.074mm accounts for 90% % of raw ore samples are subjected to flotation, such as figure 1 As shown, a roughing process is adopted for four times of selection and one sweeping process, followed by drying and magnetic separation to obtain microcrystalline graphite with a fixed carbon content of 90%;
[0057] In the raw ore treatment of this embodiment, the raw ore of microcrystalline graphite is Lutang graphite, wherein the moisture is 2.4%, the volatile matter is 2.99%, the ash content is 18.37%, and the carbon content is 78.64...
PUM
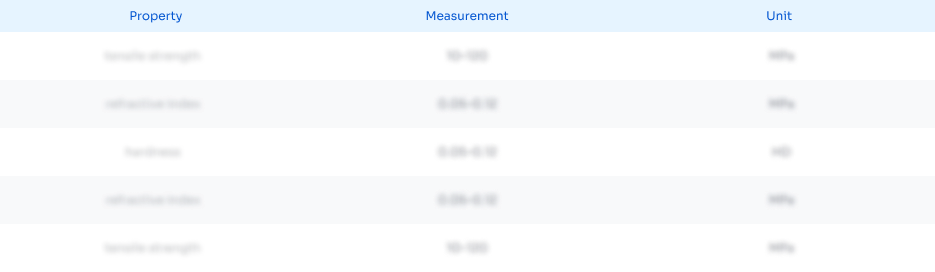
Abstract
Description
Claims
Application Information

- Generate Ideas
- Intellectual Property
- Life Sciences
- Materials
- Tech Scout
- Unparalleled Data Quality
- Higher Quality Content
- 60% Fewer Hallucinations
Browse by: Latest US Patents, China's latest patents, Technical Efficacy Thesaurus, Application Domain, Technology Topic, Popular Technical Reports.
© 2025 PatSnap. All rights reserved.Legal|Privacy policy|Modern Slavery Act Transparency Statement|Sitemap|About US| Contact US: help@patsnap.com