Incinerator for isophthalonitrile tail gas treatment
A technology for treatment of isophthalonitrile and tail gas, which is applied in the direction of incinerators, combustion methods, combustion types, etc., can solve the problems of low oxidation rate of tail gas and incomplete oxidation of waste gas, and avoid uneven internal air flow, horizontal The effect of reducing the cross-sectional area and increasing the oxidation rate
- Summary
- Abstract
- Description
- Claims
- Application Information
AI Technical Summary
Problems solved by technology
Method used
Image
Examples
Embodiment
[0029] An incineration device for isophthalonitrile tail gas treatment, its structure is as follows figure 1 As shown, it includes several oxidation beds arranged side by side and connected to each other at the upper part to form a combustion chamber. In this embodiment, there are 3, which are combined together in a vertical parallel and connected upper part to form a device body with a vertical structure. The components connected by the oxidation beds are also surrounded by a heat preservation refractory material 19. The upper parts of all the oxidizing beds connected together form the combustion chamber 20. The bottom of each oxidizing bed is provided with a supporting grid 17, and the supporting grid is provided with a ceramic rectangular saddle ring of a certain thickness, and honeycombs are stacked on the ceramic rectangular saddle ring. Ceramic heat storage body, honeycomb ceramic heat storage body is divided into high temperature zone and low temperature zone according to...
PUM
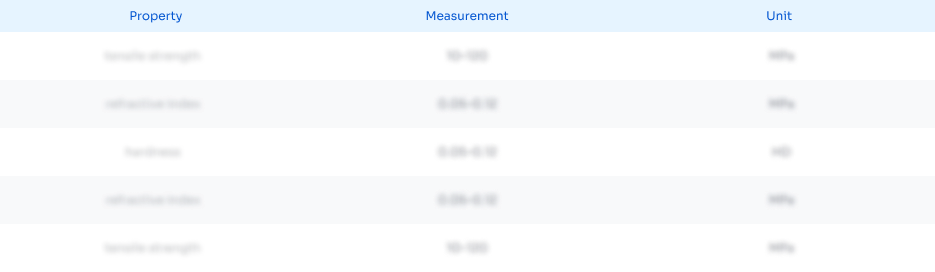
Abstract
Description
Claims
Application Information

- R&D Engineer
- R&D Manager
- IP Professional
- Industry Leading Data Capabilities
- Powerful AI technology
- Patent DNA Extraction
Browse by: Latest US Patents, China's latest patents, Technical Efficacy Thesaurus, Application Domain, Technology Topic, Popular Technical Reports.
© 2024 PatSnap. All rights reserved.Legal|Privacy policy|Modern Slavery Act Transparency Statement|Sitemap|About US| Contact US: help@patsnap.com