Three-dimensional model gradient finite element solving method based on ANSYS parametric design language
A parametric design and three-dimensional model technology, applied in the field of finite element simulation, can solve time-consuming and labor-intensive problems, and achieve the effect of improving calculation speed
- Summary
- Abstract
- Description
- Claims
- Application Information
AI Technical Summary
Problems solved by technology
Method used
Image
Examples
Embodiment Construction
[0024] In order to make the objectives, technical solutions and advantages of the present invention clearer, the following further describes the present invention in detail with reference to the accompanying drawings and embodiments. It should be understood that the specific embodiments described herein are only used to explain the present invention, but not to limit the present invention. In addition, the technical features involved in the various embodiments of the present invention described below can be combined with each other as long as they do not conflict with each other.
[0025] figure 1 It is a schematic diagram of the SOLID5 unit in the embodiment of the present invention. The unit includes eight nodes, numbered I, J, K, L, M, N, O, and P respectively. The corresponding local coordinates are (1,-1,-1),(1,1,-1),(-1,1,-1),(-1,-1,-1),(1,-1 ,1),(1,1,1),(-1,1,1),(-1,-1,1). Its shape function is:
[0026]
[0027] Where i is the node number.
[0028] figure 2 It is a sch...
PUM
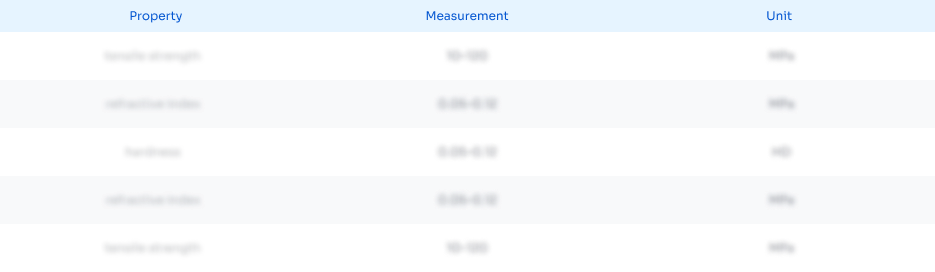
Abstract
Description
Claims
Application Information

- R&D Engineer
- R&D Manager
- IP Professional
- Industry Leading Data Capabilities
- Powerful AI technology
- Patent DNA Extraction
Browse by: Latest US Patents, China's latest patents, Technical Efficacy Thesaurus, Application Domain, Technology Topic, Popular Technical Reports.
© 2024 PatSnap. All rights reserved.Legal|Privacy policy|Modern Slavery Act Transparency Statement|Sitemap|About US| Contact US: help@patsnap.com