A kind of manufacturing method of conductive PCM board
A manufacturing method and a technology of a substrate, which are applied in the manufacture of printed circuits, removal of conductive materials through light, printed circuits, etc., can solve problems such as inability to achieve partial conduction, and achieve high removal efficiency
- Summary
- Abstract
- Description
- Claims
- Application Information
AI Technical Summary
Problems solved by technology
Method used
Examples
Embodiment Construction
[0022] The technical solution of the present invention will be further described in detail below in conjunction with specific embodiments. The present invention proposes an embodiment of a method for manufacturing a conductive PCM board. This conductive PCM board can be applied to the two-in-one inner lining board and backboard of a TV. In the backplane structure of the TV, in order to simplify the module, the inner lining board and the backplane are combined into one. In order to achieve the EMI index of the TV, the backplane of the appearance needs to be able to conduct electricity. The production of the conductive PCM board in this embodiment can meet the use requirements of the TV back panel, and realize that the front and back sides of the TV back panel can realize the conductive function at the same time. The specific steps of the manufacturing method of its corresponding conductive PCM board are as follows:
[0023] 1) Substrate pre-treatment: The substrate is first deg...
PUM
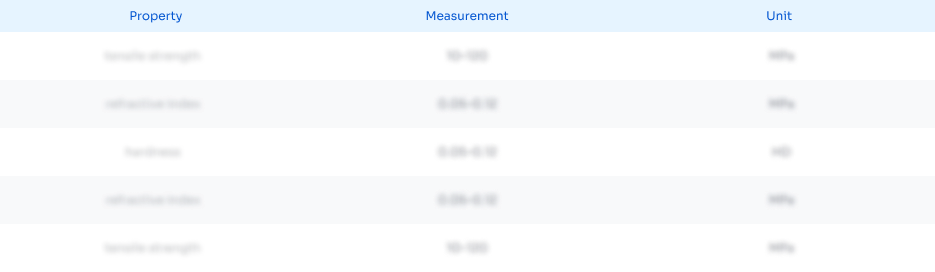
Abstract
Description
Claims
Application Information

- R&D Engineer
- R&D Manager
- IP Professional
- Industry Leading Data Capabilities
- Powerful AI technology
- Patent DNA Extraction
Browse by: Latest US Patents, China's latest patents, Technical Efficacy Thesaurus, Application Domain, Technology Topic, Popular Technical Reports.
© 2024 PatSnap. All rights reserved.Legal|Privacy policy|Modern Slavery Act Transparency Statement|Sitemap|About US| Contact US: help@patsnap.com