Foamed concrete and production process thereof
A foamed concrete and production process technology, which is applied to other household appliances, applications, household appliances, etc., can solve the problem of poor flexural resistance and freeze-thaw resistance of foamed concrete, long construction period of building exterior wall insulation, and inability to meet building thermal insulation. Engineering and other issues, to achieve the effect of shortening the solidification cycle, improving the safety performance, and shortening the solidification time
- Summary
- Abstract
- Description
- Claims
- Application Information
AI Technical Summary
Problems solved by technology
Method used
Examples
Embodiment 1
[0025] A kind of foam concrete, comprises sulfoaluminum cement, sodium metaaluminate, aluminum sulfate and hydrogen peroxide, the weight percent of each component is: 95% of sulfoaluminum cement; 0.2% of sodium metaaluminate; 0.2% of aluminum sulfate; 2% of hydrogen peroxide .
[0026] A production process of foamed concrete, wherein: comprising the following process steps:
[0027] 1. Raw material preparation;
[0028] Weigh each component by weight percentage; weigh 95% sulfur-aluminum cement; 0.2% sodium metaaluminate; 0.2% aluminum sulfate; 2% hydrogen peroxide.
[0029] 2. Stir and mix
[0030] Put the weighed sulfoaluminum cement, sodium metaaluminate and aluminum sulfate into the mixer, add water and mix them evenly.
[0031] 3. Add hydrogen peroxide into the mixer and continue mixing for 1 minute.
[0032] 4. Foam molding
[0033] Add the uniformly mixed material in step 3 into the mold for foaming, and place it for 8 minutes to allow the concrete in the mold to s...
Embodiment 2
[0036] A foamed concrete, the weight percentage of each component is sulfoaluminum cement 97.3%; sodium metaaluminate 0.1%; aluminum sulfate 0.1%; hydrogen peroxide 2.5%.
[0037] A production process of foamed concrete, wherein: comprising the following process steps:
[0038] 1. Raw material preparation;
[0039] Weigh each component by weight percentage; weigh sulfoaluminum cement 97.3% by weight percentage; sodium metaaluminate 0.1%; aluminum sulfate 0.1%; hydrogen peroxide 2.5%.
[0040] 2. Stir and mix
[0041] Put the weighed sulfoaluminum cement, sodium metaaluminate and aluminum sulfate into the mixer, add water and mix them evenly.
[0042] 3. Add hydrogen peroxide into the mixer and continue mixing for 1 minute.
[0043] 4. Foam molding
[0044] Add the uniformly mixed material in step 3 into the mold for foaming, and place it for 10 minutes to allow the concrete in the mold to solidify naturally.
[0045] 5. Demoulding, so far the production of foamed concrete...
Embodiment 3
[0047] A kind of foamed concrete, comprising sulfoaluminum cement, sodium metaaluminate, aluminum sulfate and hydrogen peroxide, the weight percent of each component is: 97% of sulfoaluminum cement; 0.05% of sodium metaaluminate; 0.05% of aluminum sulfate; 2.9% of hydrogen peroxide .
[0048] A production process of foamed concrete, wherein: comprising the following process steps:
[0049] 1. Raw material preparation;
[0050] Weigh each component by weight percentage; weigh 97% of sulfur-aluminum cement by weight percentage; 0.05% of sodium metaaluminate; 0.05% of aluminum sulfate; 2.9% of hydrogen peroxide.
[0051] 2. Stir and mix
[0052] Put the weighed sulfur-aluminum cement, sodium metaaluminate, and aluminum sulfate into the mixer, add water and mix them evenly;
[0053] 3. Add hydrogen peroxide into the mixer and continue mixing for 1 minute;
[0054] 4. Foam molding
[0055] Add the uniformly mixed material in step 3 into the mold for foaming, and place it for 1...
PUM
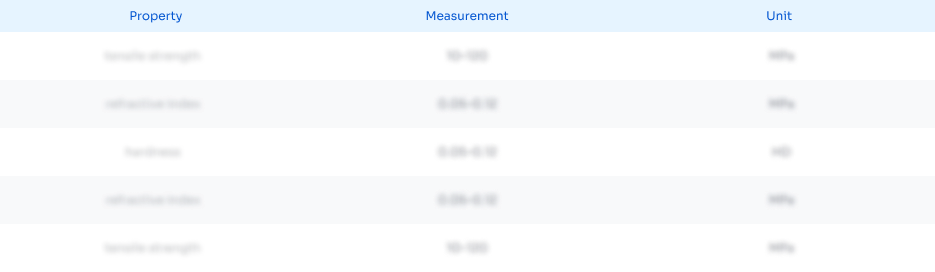
Abstract
Description
Claims
Application Information

- R&D
- Intellectual Property
- Life Sciences
- Materials
- Tech Scout
- Unparalleled Data Quality
- Higher Quality Content
- 60% Fewer Hallucinations
Browse by: Latest US Patents, China's latest patents, Technical Efficacy Thesaurus, Application Domain, Technology Topic, Popular Technical Reports.
© 2025 PatSnap. All rights reserved.Legal|Privacy policy|Modern Slavery Act Transparency Statement|Sitemap|About US| Contact US: help@patsnap.com