Hardening-time-controllable magnesium oxysulfate cement and preparation method of hardening-time-controllable magnesium oxysulfate cement plate
A technology of magnesium oxysulfide cement and hardening time, applied in the field of building materials, can solve the problems of slow curing time, low mechanical strength, unfavorable construction operations, etc., and achieve the effect of not returning to halogen and improving production efficiency
- Summary
- Abstract
- Description
- Claims
- Application Information
AI Technical Summary
Problems solved by technology
Method used
Examples
Embodiment 1
[0020] The raw materials are weighed according to the following weight ratios: 40 parts of activated magnesium oxide, 50 parts of magnesium sulfate, 1.2 parts of modifier, 7 parts of light perlite, 20 parts of water, 13 parts of hemihydrate gypsum, and 9 parts of citric acid. Lay the transfer film on the glass plate, weigh various raw materials according to the proportion, first dissolve magnesium sulfate in water, control the Baume degree at 20°C to 27, and then mix it with other weighed raw materials to form a slurry and pour it into On the transfer film, spread out, the thickness is about 10 mm. The initial setting time is 27 minutes and the final setting time is 60 minutes. The modifier is prepared by mixing sodium gluconate and sodium methyl silicate in a mass ratio of 70:30. The prepared decorative plate has no deformation, cracking and halogen reversion.
Embodiment 2
[0022] The raw materials are weighed according to the following weight ratios: 40 parts of activated magnesium oxide, 50 parts of magnesium sulfate, 1 part of modifier, 7 parts of light perlite, 20 parts of water, 15 parts of hemihydrate gypsum, and 8 parts of citric acid. Lay the transfer film on the glass plate, weigh various raw materials according to the proportion, first dissolve magnesium sulfate in water, control the Baume degree at 20°C to 27, and then mix it with other weighed raw materials to form a slurry and pour it into On the transfer film, spread out, the thickness is about 10mm. The initial setting time is 12 minutes and the final setting time is 45 minutes. The modifier is prepared by mixing sodium gluconate and sodium methyl silicate in a mass ratio of 80:20. The prepared decorative plate has no deformation, cracking and halogen reversion.
Embodiment 3
[0024] The raw materials are weighed according to the following weight ratios: 40 parts of activated magnesium oxide, 50 parts of magnesium sulfate, 0.7 parts of modifier, 7 parts of light perlite, 20 parts of water, 18 parts of hemihydrate gypsum, and 6 parts of citric acid. Lay the transfer film on the glass plate, weigh various raw materials according to the proportion, first dissolve magnesium sulfate in water, control the Baume degree at 20°C to 27, and then mix it with other weighed raw materials to form a slurry and pour it into On the transfer film, spread out, the thickness is about 10mm. The initial setting time is 8 minutes and the final setting time is 30 minutes. The modifier is prepared by mixing sodium gluconate and sodium methyl silicate in a mass ratio of 75:25. The prepared decorative plate has no deformation, cracking and halogen reversion.
PUM
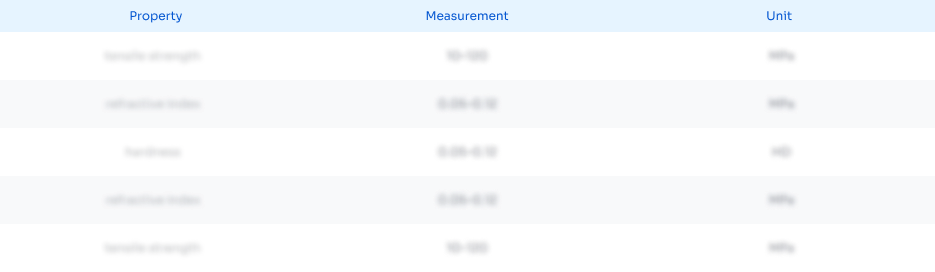
Abstract
Description
Claims
Application Information

- Generate Ideas
- Intellectual Property
- Life Sciences
- Materials
- Tech Scout
- Unparalleled Data Quality
- Higher Quality Content
- 60% Fewer Hallucinations
Browse by: Latest US Patents, China's latest patents, Technical Efficacy Thesaurus, Application Domain, Technology Topic, Popular Technical Reports.
© 2025 PatSnap. All rights reserved.Legal|Privacy policy|Modern Slavery Act Transparency Statement|Sitemap|About US| Contact US: help@patsnap.com