Preparation method of environment-friendly thermal stabilizing agent
A heat stabilizer, environmentally friendly technology, used in the plastics industry, can solve the problems of poor coloring, environmental pollution, etc., and achieve the effect of improving coloring effect, good compatibility and improving stability
- Summary
- Abstract
- Description
- Claims
- Application Information
AI Technical Summary
Problems solved by technology
Method used
Examples
example 1
[0025] In parts by weight, get 6 parts of castor oil, 3 parts of soybean oil, 1.5 parts of maleic anhydride and 3 parts of methyl ethyl ketone, add castor oil and soybean oil to a tank equipped with a thermometer, constant pressure dropping funnel, stirrer and reflux condensing Place the four-necked flask in a water bath, adjust the temperature at 55°C and preheat it for 5 minutes; pour maleic anhydride into methyl ethyl ketone, and add the obtained mixture to the constant pressure dropping funnel , dropwise into the four-necked flask at a speed of 30mL / min, after the dropwise addition, the temperature of the water bath was controlled at 75°C, stirred at a speed of 200r / min for 3h, and the solvent was removed in a vacuum to obtain a modified mixed oil; Pour the modified mixed oil into a three-necked flask equipped with a stirrer, a thermometer and a constant pressure dropping funnel, pour 50% of the modified mixed oil into formic acid, 20% of the modified mixed oil in dibenzoyl...
example 2
[0027]In parts by weight, get 7 parts of castor oil, 3 parts of soybean oil, 1.8 parts of maleic anhydride and 3 parts of methyl ethyl ketone, add soybean oil and castor oil to a tank equipped with a thermometer, constant pressure dropping funnel, stirrer and reflux condensing Place the four-necked flask in a water bath, adjust the temperature at 60°C and preheat for 8 minutes; pour maleic anhydride into methyl ethyl ketone, and add the obtained mixture to the constant pressure dropping funnel , dropwise into the four-neck flask at a speed of 30mL / min, after the dropwise addition, the temperature of the water bath was controlled at 78°C, stirred at a speed of 240r / min for 3h, and the solvent was removed in a vacuum to obtain a modified mixed oil; Pour the modified mixed oil into a three-necked flask equipped with a stirrer, a thermometer and a constant pressure dropping funnel, pour 50% of the modified mixed oil into formic acid, 20% of the modified mixed oil in dibenzoylmethan...
example 3
[0029] In parts by weight, take 8 parts of castor oil, 4 parts of soybean oil, 2.0 parts of maleic anhydride and 4 parts of methyl ethyl ketone, and add castor oil and soybean oil to a tank equipped with a thermometer, constant pressure dropping funnel, stirrer and reflux condensing Place the four-necked flask in a water bath, adjust the temperature at 65°C and preheat it for 10 minutes; pour maleic anhydride into methyl ethyl ketone, and add the obtained mixture to the constant pressure dropping funnel , dropwise into the four-neck flask at a speed of 30mL / min, after the dropwise addition, the temperature of the water bath was controlled at 80°C, stirred at a speed of 280r / min for 4h, and the solvent was removed in a vacuum to obtain a modified mixed oil; Pour the modified mixed oil into a three-necked flask equipped with a stirrer, a thermometer and a constant pressure dropping funnel, pour 50% of the modified mixed oil into formic acid, 20% of the modified mixed oil in diben...
PUM
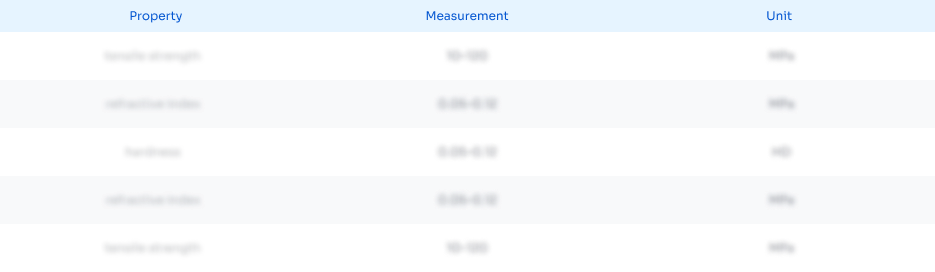
Abstract
Description
Claims
Application Information

- Generate Ideas
- Intellectual Property
- Life Sciences
- Materials
- Tech Scout
- Unparalleled Data Quality
- Higher Quality Content
- 60% Fewer Hallucinations
Browse by: Latest US Patents, China's latest patents, Technical Efficacy Thesaurus, Application Domain, Technology Topic, Popular Technical Reports.
© 2025 PatSnap. All rights reserved.Legal|Privacy policy|Modern Slavery Act Transparency Statement|Sitemap|About US| Contact US: help@patsnap.com