Technology for producing diisobutylene from C4 mixture
A technology of mixing carbon tetra and diisobutene, which is applied in the chemical industry, hydrocarbons, hydrocarbons, etc., can solve the problems of complex process, increase energy consumption, reduce isobutene concentration, etc., achieve high reaction selectivity and reduce investment. , the effect of saving energy
- Summary
- Abstract
- Description
- Claims
- Application Information
AI Technical Summary
Problems solved by technology
Method used
Image
Examples
Embodiment 1
[0037] see figure 1 In the process flow shown, the D006 type macroporous strong acid cation exchange resin is used as the catalyst for the dimerization reaction, at a pressure of 0.60MPa, a temperature of 60°C, an addition of tert-butanol of 1% of the amount of mixed carbon tetra, and a space velocity of 0.90 h -1 Under the condition of , the polymerization reaction was carried out, the conversion rate of isobutene was 94%, and the selectivity of diisobutene was 99.2%. The reacted material enters the rectification tower to continue the separation of reactants and products. Under the conditions of a pressure of 0.40Mpa and a reflux ratio of 2.2, the unreacted mixed carbon four is discharged from the top of the tower, and the diisobutylene product with high purity (≥99.2%) is obtained in the tower reactor.
Embodiment 2
[0039] see figure 1 In the process flow shown, the D006 type macroporous strong acid cation exchange resin is used as the catalyst for the dimerization reaction, at a pressure of 0.50MPa, a temperature of 50°C, an addition of tert-butanol is 0.7% of the amount of mixed carbon four, and a space velocity of 1.20 h -1 Under the conditions of the polymerization reaction, the conversion rate of isobutene is 92.5%, and the selectivity of diisobutene is 99.3%. The reacted material enters the rectification tower to continue the separation of reactants and products. Under the conditions of a pressure of 0.40Mpa and a reflux ratio of 1.5, the unreacted mixed carbon four is discharged from the top of the tower, and a diisobutylene product with high purity (≥99.1%) is obtained in the tower reactor.
Embodiment 3
[0041] see figure 1 In the process flow shown, the D006 type macroporous strong acid cation exchange resin is used as the catalyst for the dimerization reaction, at a pressure of 0.40 MPa, a temperature of 40°C, an addition of tert-butanol of 2% of the amount of mixed carbon four, and a space velocity of 2.0 h -1 Under the conditions of the polymerization reaction, the conversion rate of isobutene is 91%, and the selectivity of diisobutene is 99.3%. The reacted material enters the rectification tower to continue the separation of reactants and products. Under the conditions of a pressure of 0.35Mpa and a reflux ratio of 2.0, the unreacted mixed carbon four is discharged from the top of the tower, and a diisobutylene product with high purity (≥99.3%) is obtained in the tower reactor.
PUM
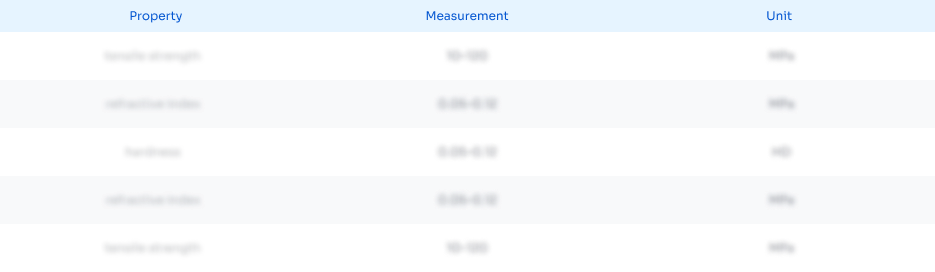
Abstract
Description
Claims
Application Information

- R&D
- Intellectual Property
- Life Sciences
- Materials
- Tech Scout
- Unparalleled Data Quality
- Higher Quality Content
- 60% Fewer Hallucinations
Browse by: Latest US Patents, China's latest patents, Technical Efficacy Thesaurus, Application Domain, Technology Topic, Popular Technical Reports.
© 2025 PatSnap. All rights reserved.Legal|Privacy policy|Modern Slavery Act Transparency Statement|Sitemap|About US| Contact US: help@patsnap.com