Polymethacrylimide foam plastic and preparation method thereof
A polymethacrylimide and foamed plastic technology, which is applied in the chemical industry and can solve the problems such as the inability of the polymethacrylimide foamed plastic to degrade.
- Summary
- Abstract
- Description
- Claims
- Application Information
AI Technical Summary
Problems solved by technology
Method used
Examples
preparation example Construction
[0040] In addition, the present invention also provides a kind of preparation method of above-mentioned polymethacrylimide foamed plastics, comprises steps:
[0041] S1. Mix the raw materials to obtain initial materials.
[0042] The main ingredients in this embodiment are methacrylic acid and methacrylonitrile. During the production process, the main ingredients are fully mixed with other various additives. It should be understood that in this example, the various raw materials should be fully mixed to make them evenly distributed, so that the reaction can be more complete, which can be achieved by prolonging the mixing time or increasing the stirring speed. It should be understood that the specific equipment used and For the mixing method, reference can be made to the existing and improved mixing equipment and methods, which are not the invention point of the present invention, so details are not repeated here.
[0043] S2. Pour the initial material into a closed container,...
Embodiment 1
[0050] Main ingredients: 55 parts of methacrylic acid, 25 parts of methacrylonitrile;
[0051] Foaming agent: AC, 0.5 part;
[0052] Initiator: benzoyl peroxide, 0.8 part;
[0053] Nucleating agent: sodium phenylphosphate, 0.02 parts;
[0054] Coupling agent: KH-550, 0.01 parts;
[0055] Pre-recovery agent: CPE, 1 part;
[0056] Concrete preparation steps include:
[0057] Step 1, weighing the above-mentioned raw materials according to the above-mentioned ratio, mixing, and stirring evenly to obtain the initial material;
[0058] Step 2, inject the initial material obtained in step 1 into a closed container, and then place the closed container in a water bath for polymerization to obtain a foam matrix, wherein the temperature of the water bath is controlled at 32 degrees Celsius, and the polymerization reaction time is 20 hours;
[0059] Step 3. Preheat the foam base prepared in step 2 in an air oven at 160 degrees Celsius for 0.5 hours, then foam at 200 degrees Celsius f...
Embodiment 2
[0061] Main ingredients: 75 parts of methacrylic acid, 45 parts of methacrylonitrile;
[0062] Foaming agent: DPT, 3 parts;
[0063] Initiator: dicyclohexyl peroxydicarbonate, 2 parts;
[0064] Nucleating agent: sodium phenylphosphate, 1 part;
[0065] Coupling agent: A-172, 2 parts;
[0066] Pre-recovery agent: EEP, 2 parts;
[0067] Concrete preparation steps include:
[0068] Step 1, weighing the above-mentioned raw materials according to the above-mentioned ratio, mixing, and stirring evenly to obtain the initial material;
[0069] Step 2, inject the initial material obtained in step 1 into a closed container, and then place the closed container in an oil bath for polymerization to obtain a foam matrix, wherein the temperature of the oil bath is controlled at 47 degrees Celsius, and the polymerization reaction time is 55 hours;
[0070] Step 3. Preheat the foam base prepared in step 2 in an air oven at 190 degrees Celsius for 5 hours, then foam at 240 degrees Celsius fo...
PUM
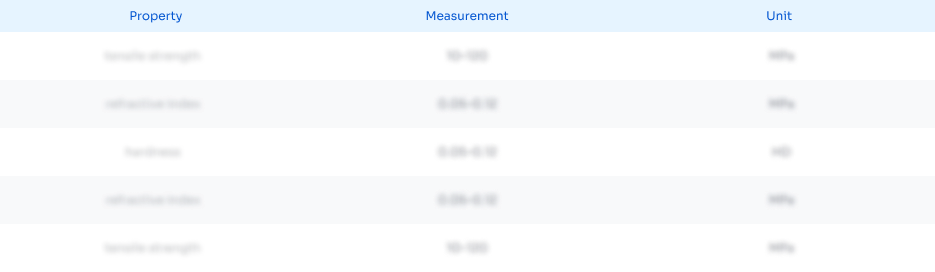
Abstract
Description
Claims
Application Information

- R&D
- Intellectual Property
- Life Sciences
- Materials
- Tech Scout
- Unparalleled Data Quality
- Higher Quality Content
- 60% Fewer Hallucinations
Browse by: Latest US Patents, China's latest patents, Technical Efficacy Thesaurus, Application Domain, Technology Topic, Popular Technical Reports.
© 2025 PatSnap. All rights reserved.Legal|Privacy policy|Modern Slavery Act Transparency Statement|Sitemap|About US| Contact US: help@patsnap.com