Method for improving machining precision of reverse extrusion female die of outer joint
A technology of processing precision and external joints, applied in metal processing equipment, metal extrusion forming tools, metal extrusion, etc., can solve the problem of unstable gap between the punch and the die and the inability to accurately guarantee the size of the die mouth , can not guarantee the high precision of the mold and other problems, to achieve the effect of simple processing method, suitable for popularization and application, and enhance the corporate image
- Summary
- Abstract
- Description
- Claims
- Application Information
AI Technical Summary
Problems solved by technology
Method used
Image
Examples
Embodiment Construction
[0025] A method for improving the processing accuracy of an external joint reverse extrusion die, comprising the following steps:
[0026] Saw material, according to the total length of the finished product, leave a margin at both ends of the mold steel raw material bar; specifically, leave a margin of 5-10mm at both ends of the total length of the finished product from the mold steel raw material bar The blank is sawed up and down.
[0027] Rough turning, according to the total length of the finished product, the rough turning process is carried out on the blank with a margin of 0.5-1 mm left at both ends of the total length of the finished product.
[0028] Quenching, heat treatment on the mold that has been roughed to increase the hardness of the material and improve the performance of the mold.
[0029] Finish turning, according to the set size, carry out finish turning processing on the mold.
[0030] Rough milling, the size of the inner cavity of the mold is milled out...
PUM
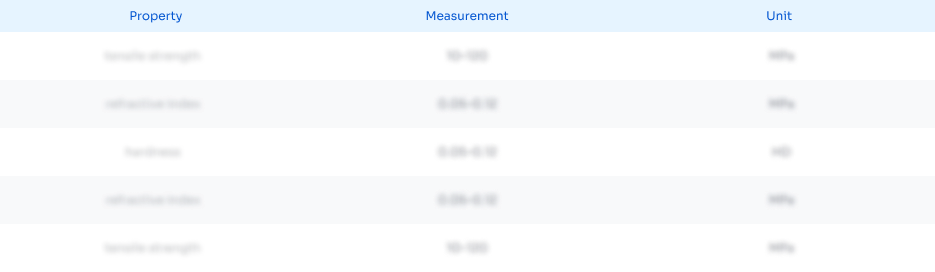
Abstract
Description
Claims
Application Information

- Generate Ideas
- Intellectual Property
- Life Sciences
- Materials
- Tech Scout
- Unparalleled Data Quality
- Higher Quality Content
- 60% Fewer Hallucinations
Browse by: Latest US Patents, China's latest patents, Technical Efficacy Thesaurus, Application Domain, Technology Topic, Popular Technical Reports.
© 2025 PatSnap. All rights reserved.Legal|Privacy policy|Modern Slavery Act Transparency Statement|Sitemap|About US| Contact US: help@patsnap.com