Integrated lathe rough-finish machining system for intaglio roller
A technology for lathe processing and gravure plate rolls, which is applied in metal processing equipment, metal processing mechanical parts, turning equipment, etc., can solve the problem that the numerical control system and the supporting servo drive motor position feedback value transmission, processing accuracy and processing efficiency are difficult to improve. , the limited application range of automatic measurement methods, etc., to shorten the auxiliary time of the machine tool, prolong the accuracy retention time, and reduce the noise.
- Summary
- Abstract
- Description
- Claims
- Application Information
AI Technical Summary
Problems solved by technology
Method used
Image
Examples
Embodiment
[0034] Such as figure 1 As shown, a gravure plate roller roughing and finishing integrated lathe processing system, the system includes a machine tool base 1, an inclined workbench 2 and a horizontal workbench 3 arranged on the machine tool base 1, and a The rotating shaft 4, the drive motor connected to the rotating shaft 4, the tool adjustment detection unit movably arranged on the horizontal worktable 3 through the X-direction feed transmission mechanism, and the drive motor, the X-direction feed transmission mechanism and the tool respectively An electrical controller that regulates the electrical connection of the detection unit. The driving motor is provided with a torque sensor electrically connected with the electric controller.
[0035] Such as figure 2 As shown, the X-direction feed transmission mechanism includes a linear motor, a grating ruler 5 arranged opposite to the linear motor, a linear guide rail 6 arranged on the horizontal worktable 3 along the horizont...
PUM
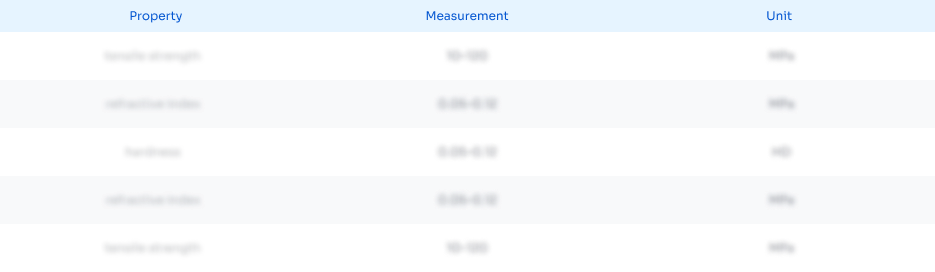
Abstract
Description
Claims
Application Information

- R&D
- Intellectual Property
- Life Sciences
- Materials
- Tech Scout
- Unparalleled Data Quality
- Higher Quality Content
- 60% Fewer Hallucinations
Browse by: Latest US Patents, China's latest patents, Technical Efficacy Thesaurus, Application Domain, Technology Topic, Popular Technical Reports.
© 2025 PatSnap. All rights reserved.Legal|Privacy policy|Modern Slavery Act Transparency Statement|Sitemap|About US| Contact US: help@patsnap.com